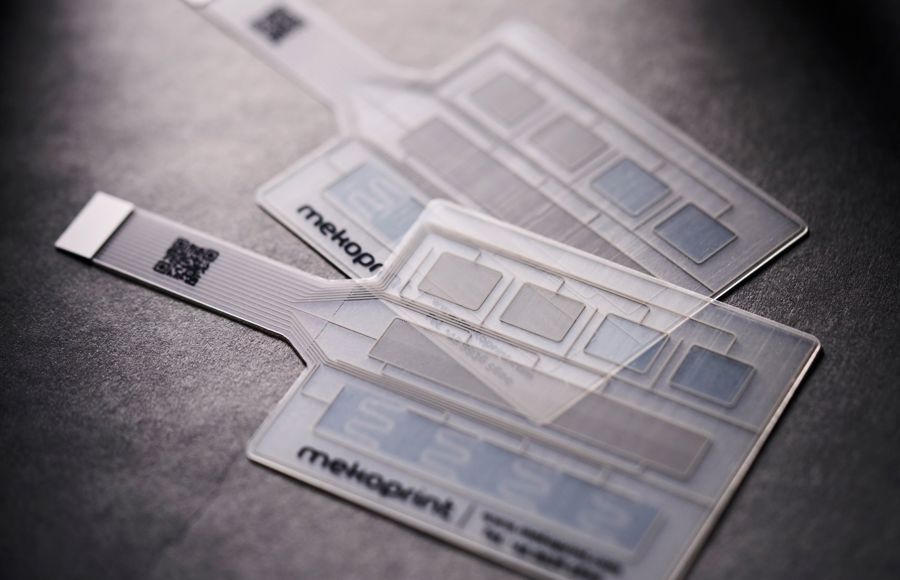
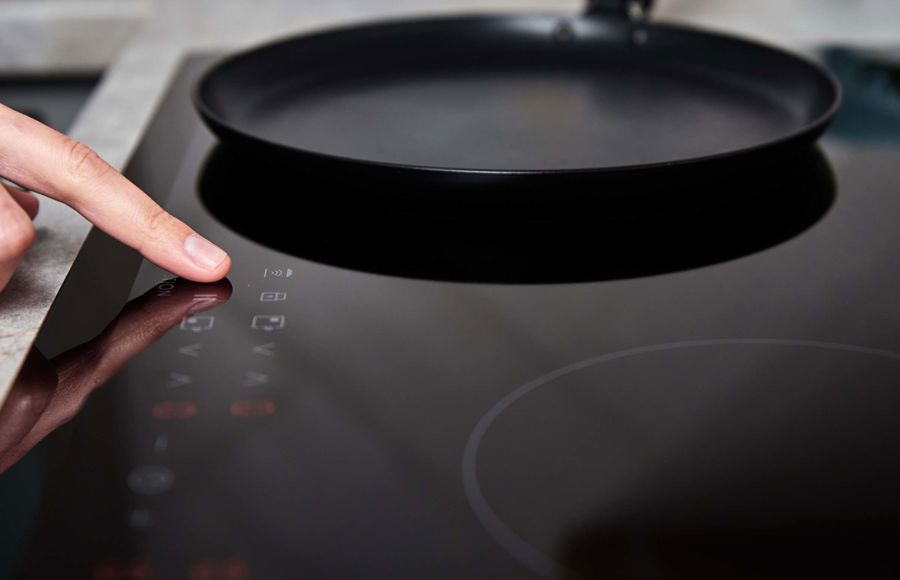
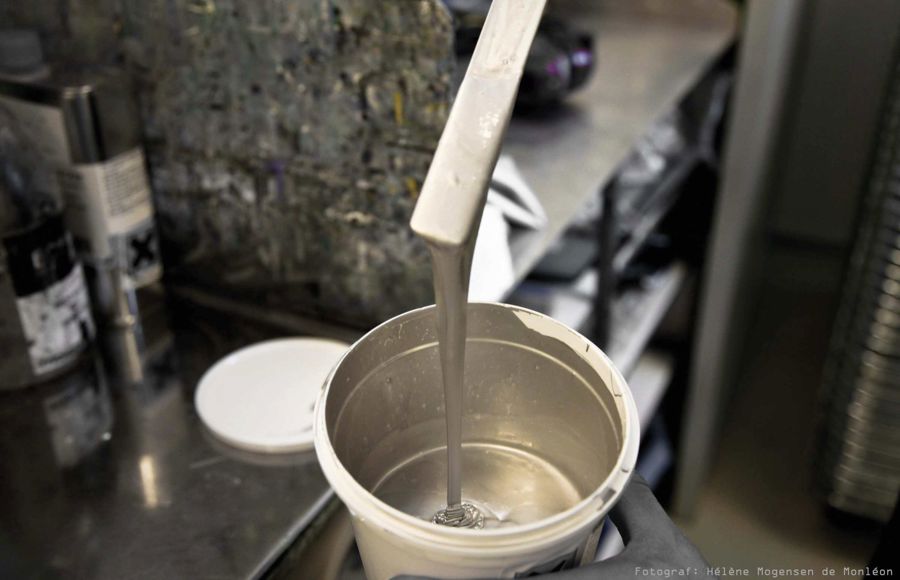
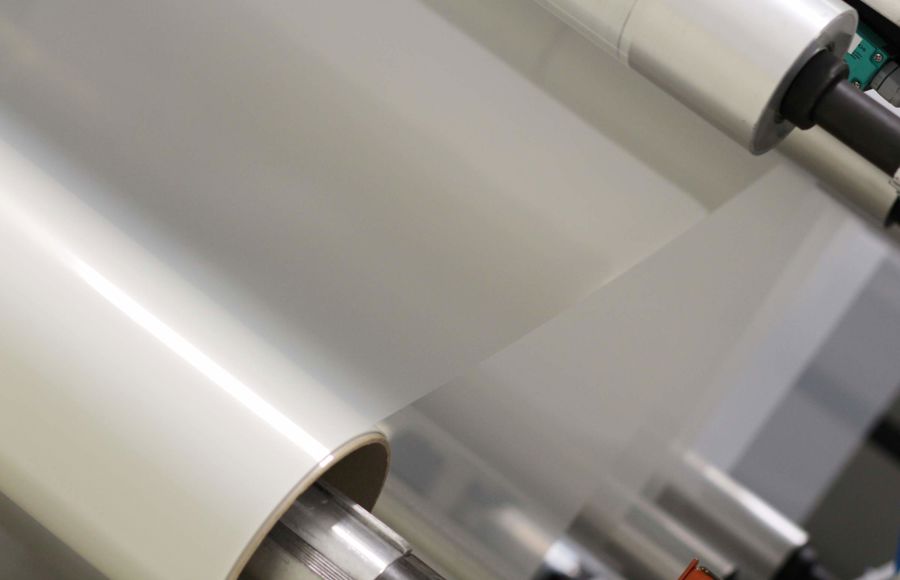
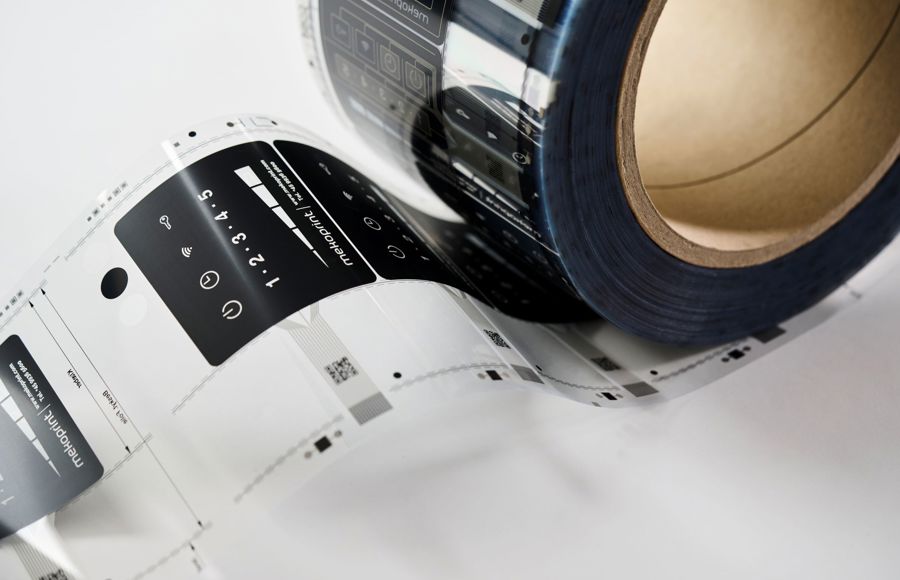
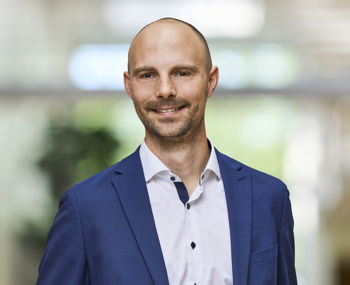
Get in touch with us
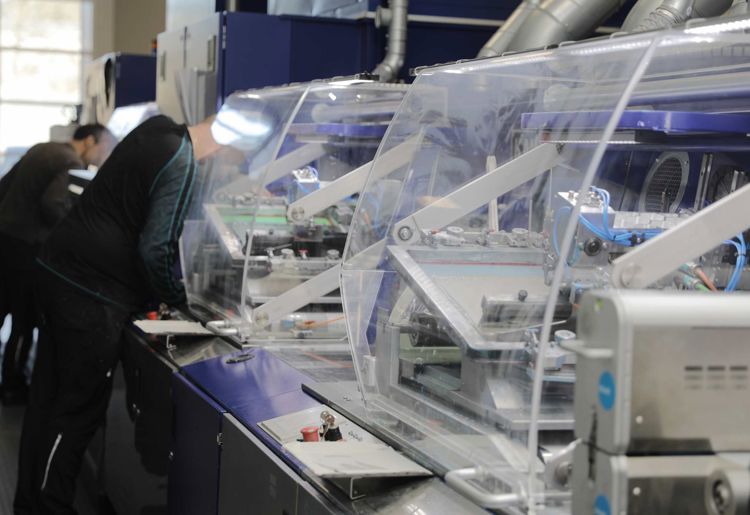
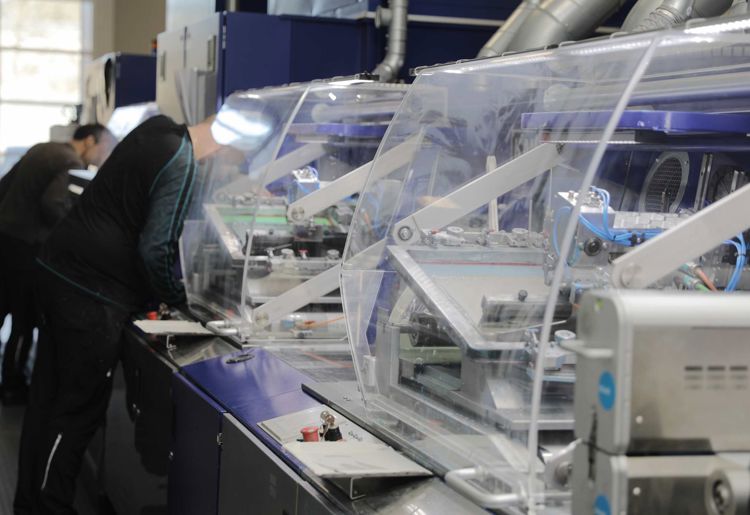
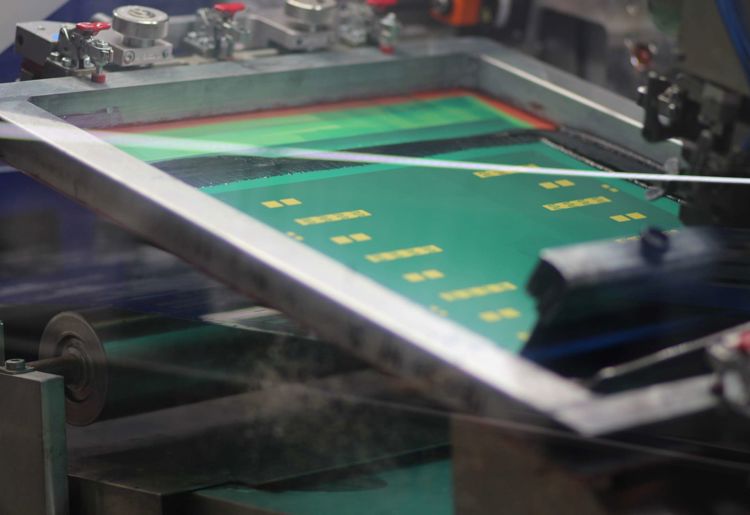
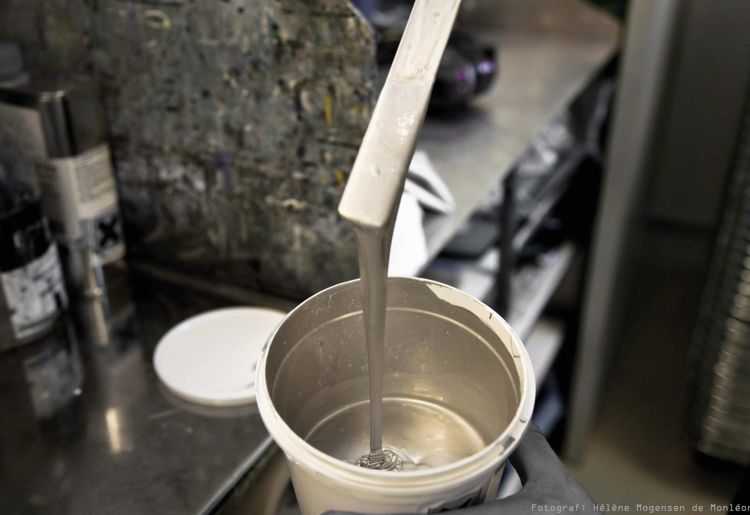
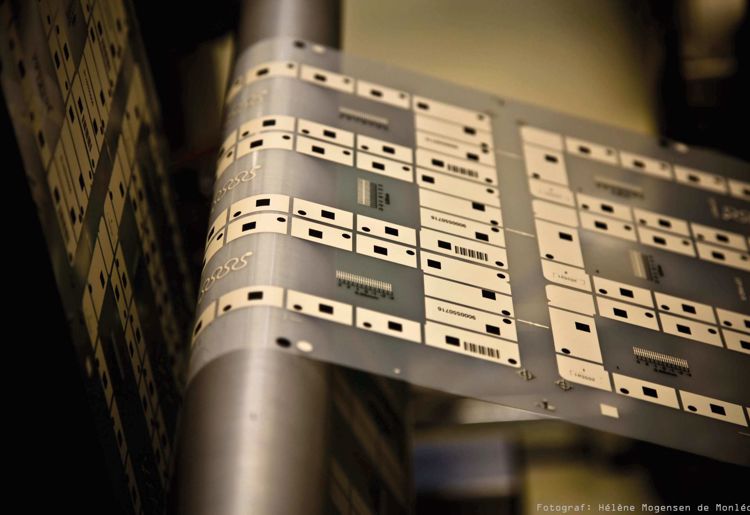
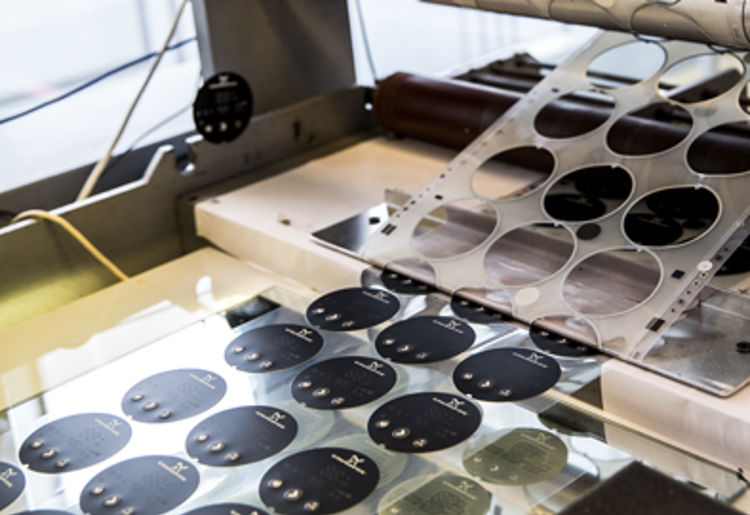
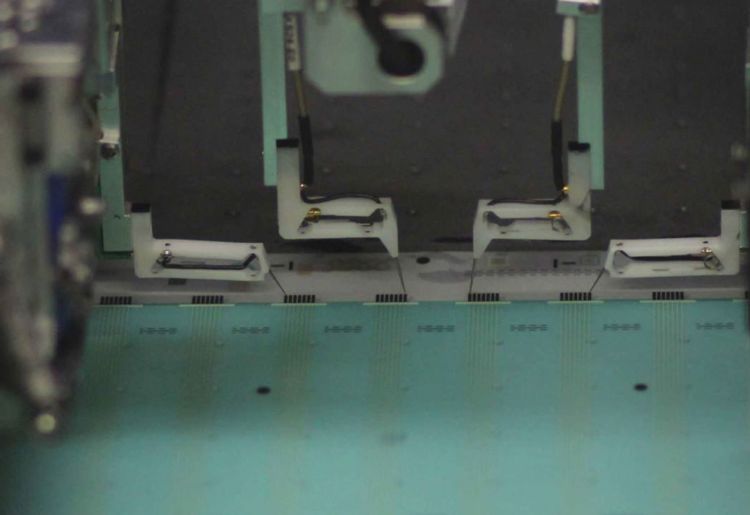
-
Our fully automated roll-to-roll screen printing process ensures high-volume, consistent, and precise sensor manufacturing. With five multi-station roll-to-roll printing lines, we produce kilometers of sensors daily, making us a leader in printed electronics.
Read more about our manufacturing process of printed electronic components.
-
The choice of substrate materials is critical in printed electronics, influencing sensor performance, flexibility, and durability. Our high-quality substrates include:
-
Polyester (PET) – Cost-effective with excellent insulation properties.
-
Polycarbonate (PC) – Impact-resistant for demanding environments.
-
Polyethylene Naphthalate (PEN) – Superior heat resistance and mechanical stability.
-
Non-woven materials – Ideal for stretchable, breathable applications.
-
TPU foil – Stretchable and elastic, perfect for wearables and flexible sensors.
-
-
Our automated sensor production includes:
-
Single and double-sided printing for increased design flexibility.
-
1, 2, and 3-section printing enabling multi-layered structures for advanced electronic applications.
-
-
We support a variety of roll-to-roll formats:
-
Roll width up to 750 mm
-
Roll lengths from 250 meters to several kilometers
-
Material thicknesses ranging from 50 to 500 μm
-
Line widths and spacing down to 50 μm, ensuring high-precision circuit patterns
-
-
To optimize sensor production, we provide advanced roll-to-roll finishing with minimal manual handling. Our finishing techniques include:
-
Die-cutting ensures precise component cutting for seamless assembly.
-
Laser cutting delivers high-precision, burr-free edges for complex designs.
-
Embossing adds raised textures for improved usability.
-
Laminating enhances durability and protection against environmental factors.
-
Slitting provides custom roll widths for specific production needs.
-
Electrical testing ensures optimal sensor performance before delivery.
-
-
We integrate flying-probe electrical testing to verify high-volume sensor functionality, ensuring reliability through:
-
Capacitance testing verifies electrical storage properties.
-
Resistance testing ensures circuit integrity.
-
Inductance testing evaluates energy storage capacity.
-
Open circuit detection identifies breaks in conductive paths.
-
Short circuit detection prevents unintended electrical connections.
-
Component testing confirms the functionality of integrated elements.
Depending on requirements, we conduct complete electrical test of sensors on final production batch and/or regular testing throughout the manufacturing process to detect potential defects early.
-
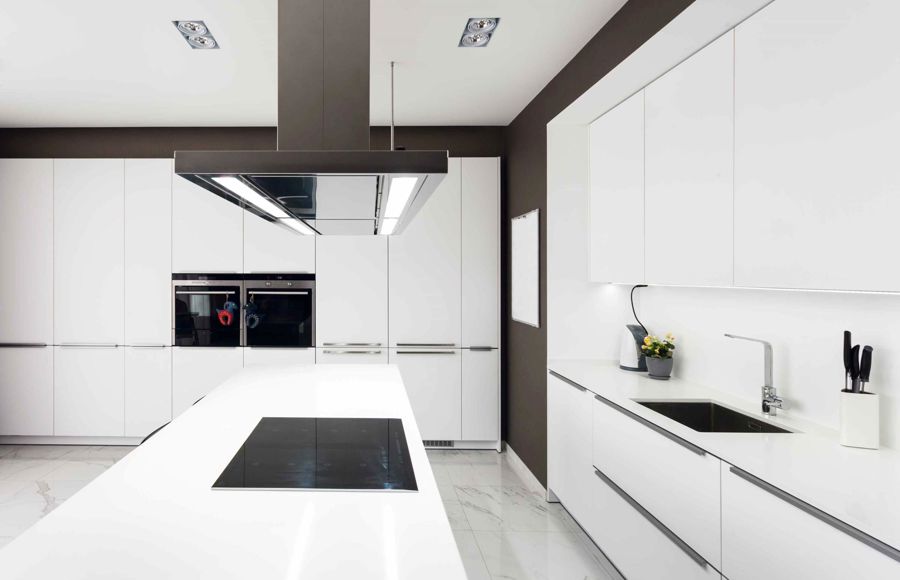
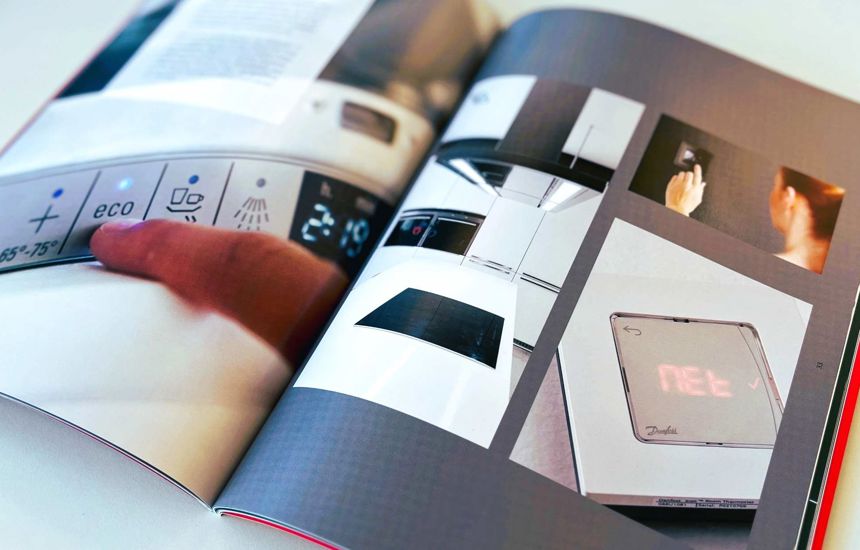
Download free lookbook
Expanding possibilities with capacitive touch sensors
Capacitive touch sensors enable innovative solutions across industries, enhancing user experience and functionality. From home appliances with seamless touch controls to robotics with artificial skin-like sensing, these sensors redefine how we interact with technology. They drive automotive innovation, enhance wearable technology, and improve medical device monitoring, making them essential for modern, responsive interfaces.
-
Home appliances with improved user experience by replacing traditional buttons with smooth, touch-sensitive controls.
-
Robotics with sensors acting as artificial skin, allowing robots to detect object interactions with precision.
-
Automotive innovation with redefined car interiors by replacing mechanical buttons with sleek, responsive panels.
-
Wearable technology utilize capacitive sensing to accurately measure body movements and pressure changes.
-
Medical device monitoring of pressure distribution on patients or surfaces.
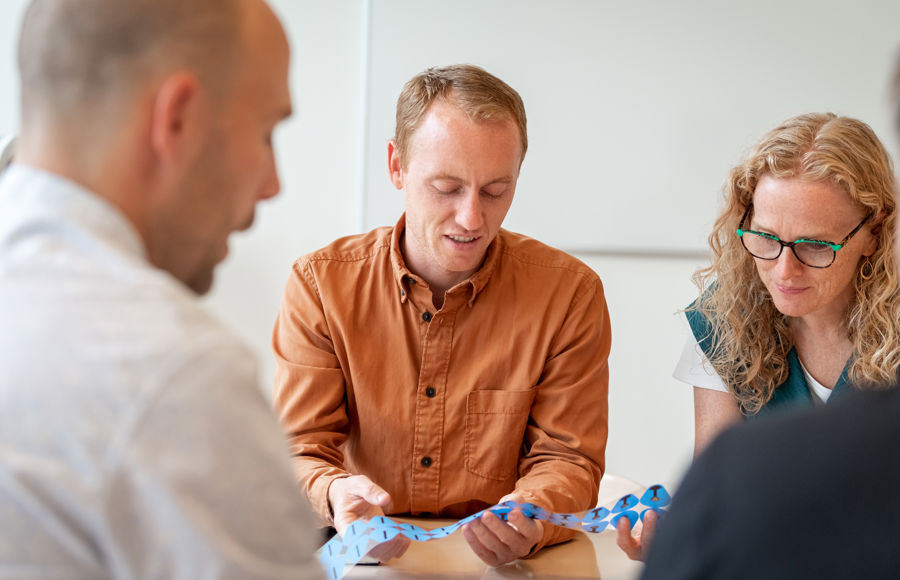
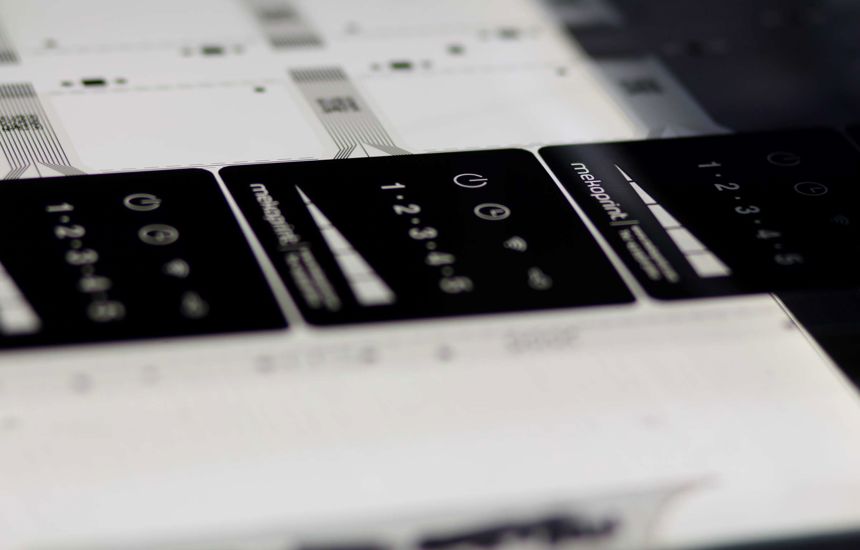
Order free product sample
-
Development, production maturation, and large-scale production in collaboration with our engineering team.Engineering printed electronics
-
Automated manufacturing of large-scale printed electronic sensors and circuits with uniform design.Production of printed electronics
-
Automated electrical function test of printed electronic components on rolls. Tailored to each individual project.Test of printed electronics
-
Ultra-thin wearable sensors ideal for single-use health care applications. Brings electronics close to the body.Wearable sensors
-
Flexible circuits cut down on space and weight. Ideal for devices where a rigid circuit board will be impractical.Flexible circuits
-
Lightweight and thin printed heaters. Flexible structure, easy to integrate and tailored to any shape and size.Printed heaters
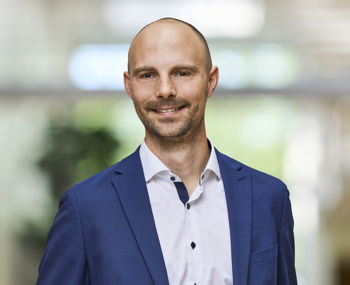