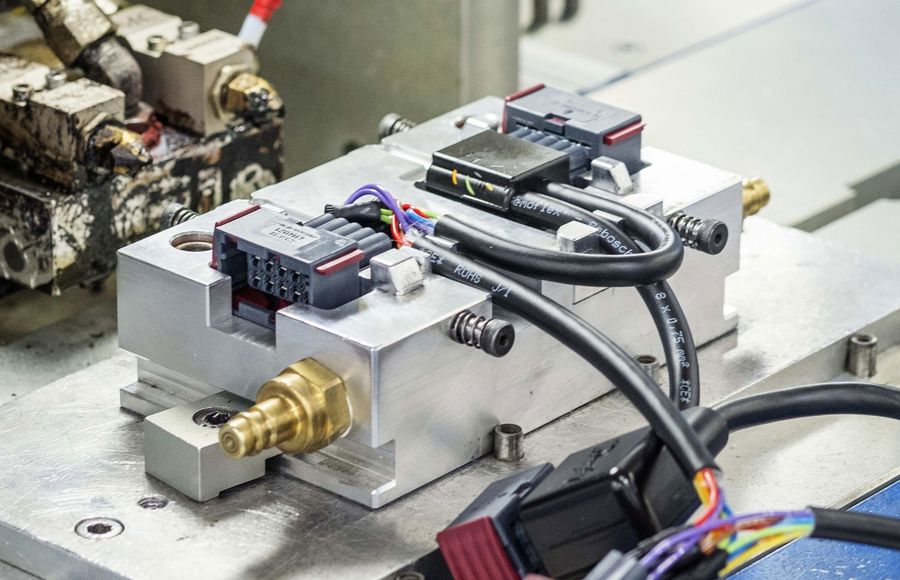
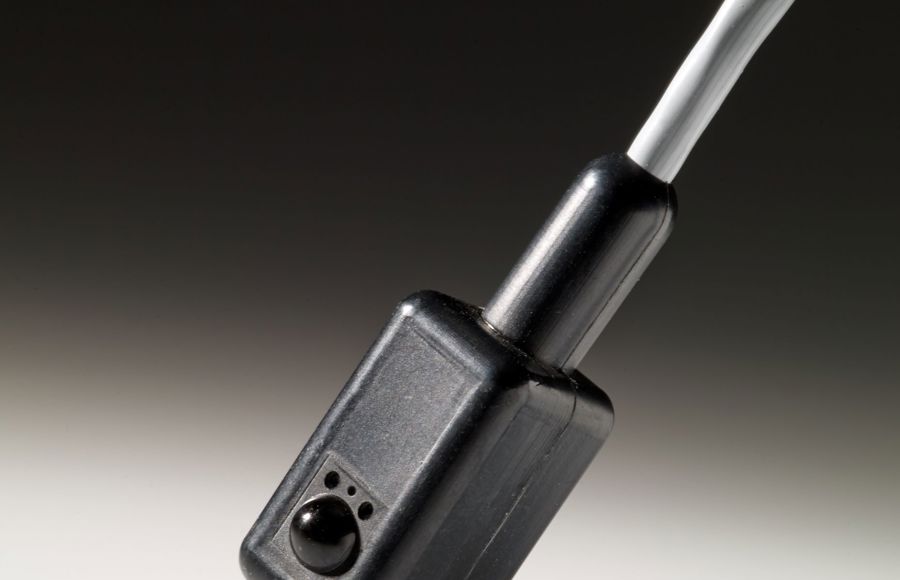
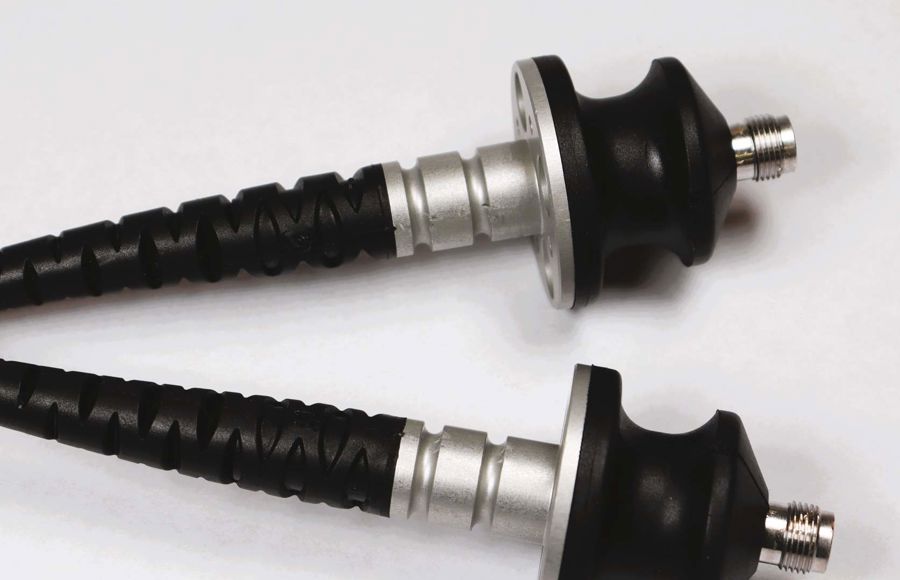

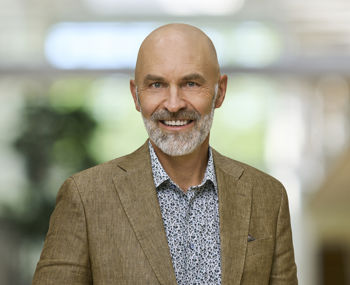
Get in touch with us
Low-Pressure Injection Molding
Low-pressure injection molding is ideal for small-scale and sensitive electronics. It uses polyamide material injected at low pressure and temperature to encapsulate components without causing damage.
The process is efficient, cost-effective, and well-suited for prototypes and mid-volume production of custom molded cables - especially when sealing connectors or delicate circuitry.
.
Materials
The primary material used is Technomelt (previously known as Macromelt), a thermoplastic polyamide that’s sustainable, cost-efficient, and environmentally friendly. Made from 80% renewable raw materials, it provides excellent electrical insulation and chemical stability.
Technomelt complies with UL, RoHS, and REACH standards, making it a reliable choice for high-performance cable assemblies.
Process
Low-pressure molding works at pressures under 100 psi and temperatures between 170°C and 240°C, reducing the risk of damaging sensitive electronics. It allows for the creation of custom-shaped overmolds, connector sealing, and functional reliefs.
The use of aluminum tooling further reduces costs and speeds up production. This method is also ideal for achieving IP-rated sealing and integrating molded cables into complex assemblies.
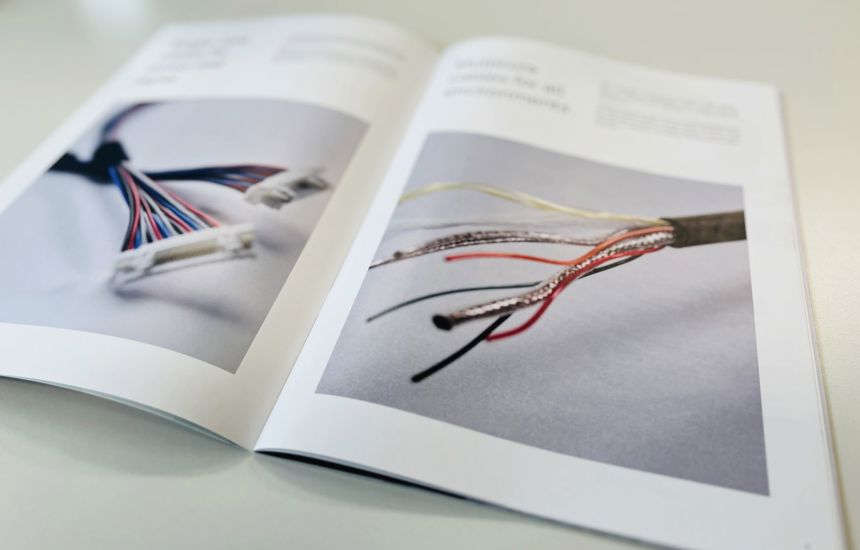
Download free lookbook
High-pressure injection molding
High-pressure injection molding is the preferred method for applications requiring strong mechanical performance and robust environmental sealing.
This process uses thermoplastic materials injected at high pressure to form molded cable assemblies with excellent resistance to impact, chemicals, and temperature fluctuations. It’s ideal for mass production and for cable assemblies operating in harsh environments where long-term durability is essential.
.
Materials
A wide range of thermoset materials can be used, including TPE, TPU, and PVC compounds—each selected for their specific mechanical and chemical properties. Reinforced options like PBT with fiberglass, ABS, or PVC enhance strength, flexibility, and heat resistance.
Material choice is guided by your specific requirements for temperature range, adhesion, elasticity, and even color to ensure optimal performance and compatibility.
Process
High-pressure molding excels at producing complex, detailed shapes while fully encapsulating connectors and electronic components. The high pressure and temperature allow for tight dimensional control, precision features, and high-quality surface finishes. It creates a reliable seal against water, dust, moisture, and heat, contributing to overall product longevity and performance.
The use of this process also reduces the need for post-processing, thanks to the smooth finish and consistent texture of molded parts—improving both efficiency and the appearance of the final assembly.
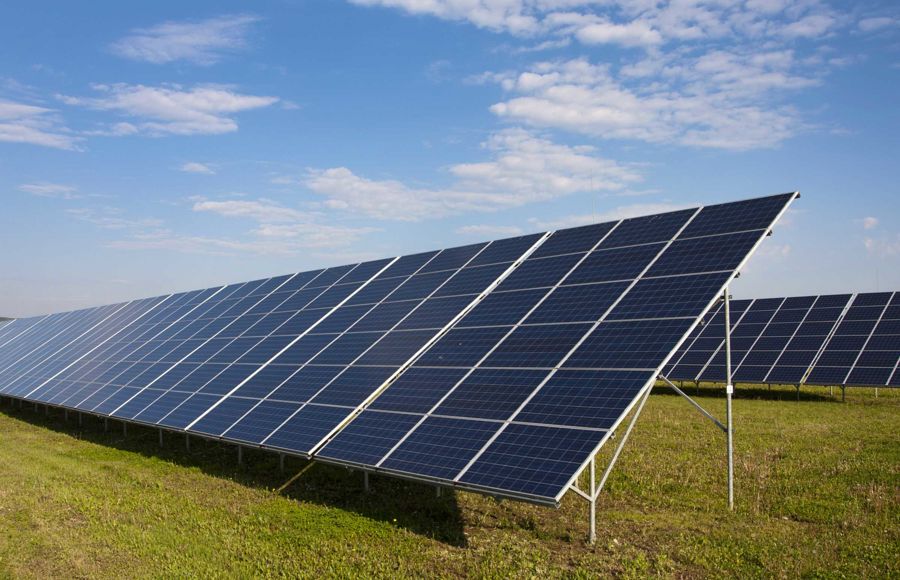
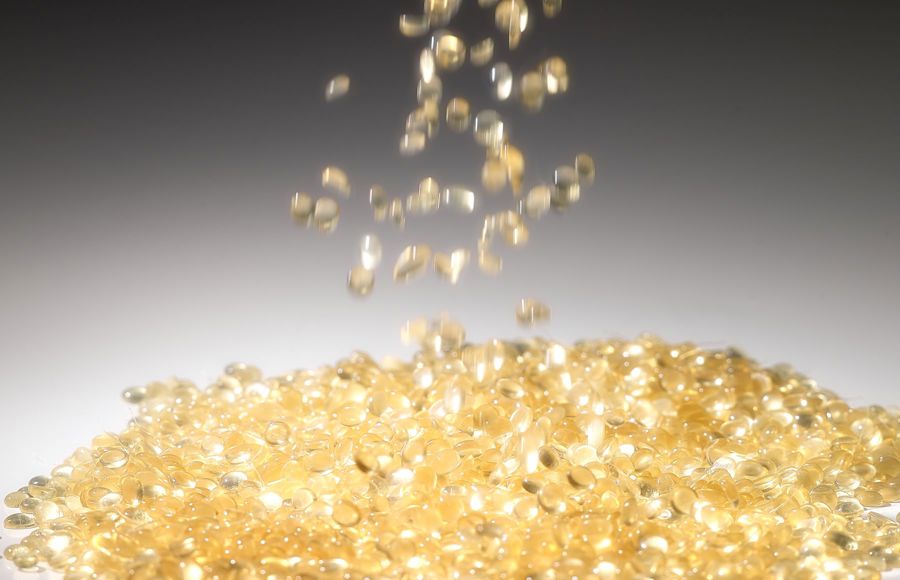
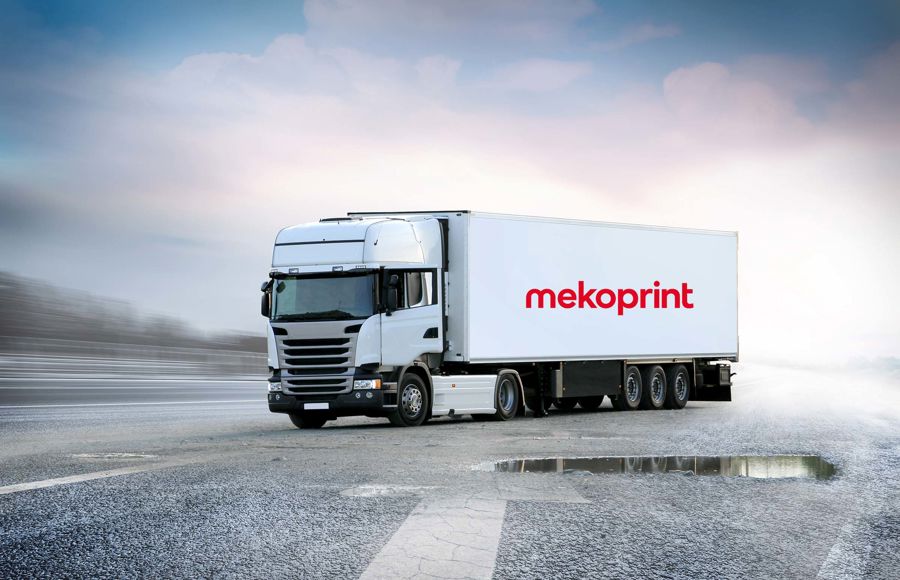
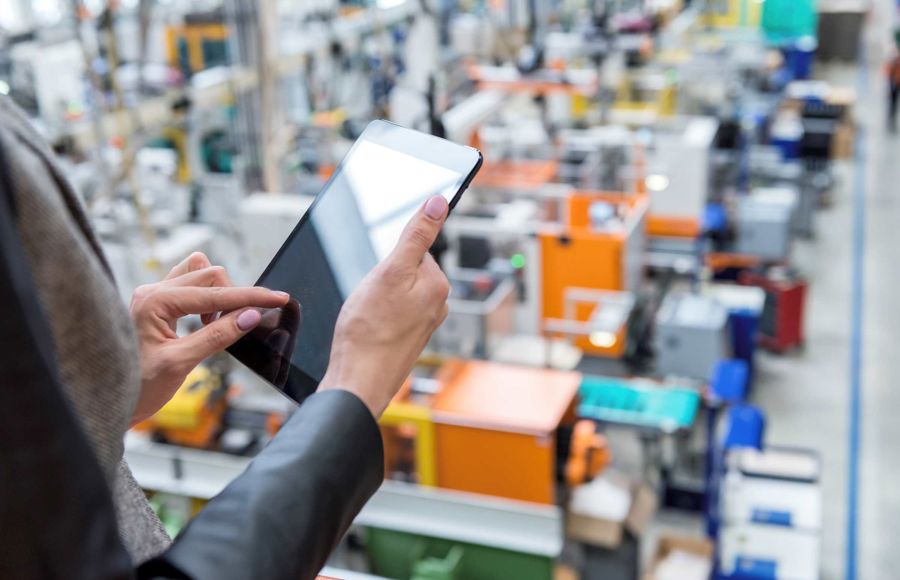

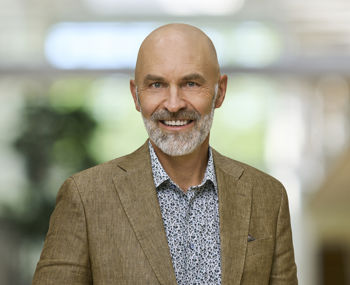
Get in touch with us
-
Multiple insulated conductors bundled together in a single cable structure for enhanced space-saving and efficiency.Multicore cables
-
Single conductors of copper or aluminium, encased in a protective insulation layer, w/o terminals and labelling.Single core cables
-
Heavy cables with thick insulation and robust conductors built to endure high electrical currents and mechanical stress.Heavy cables