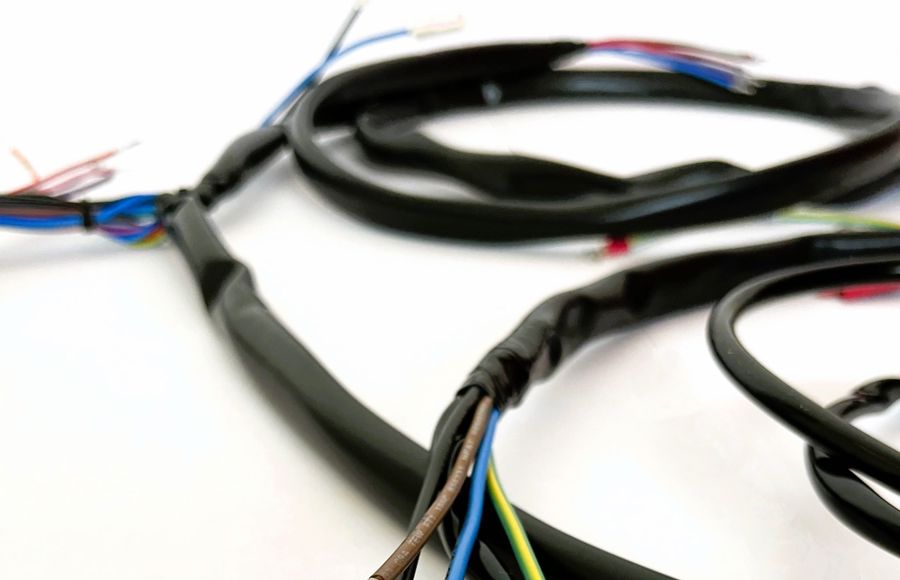
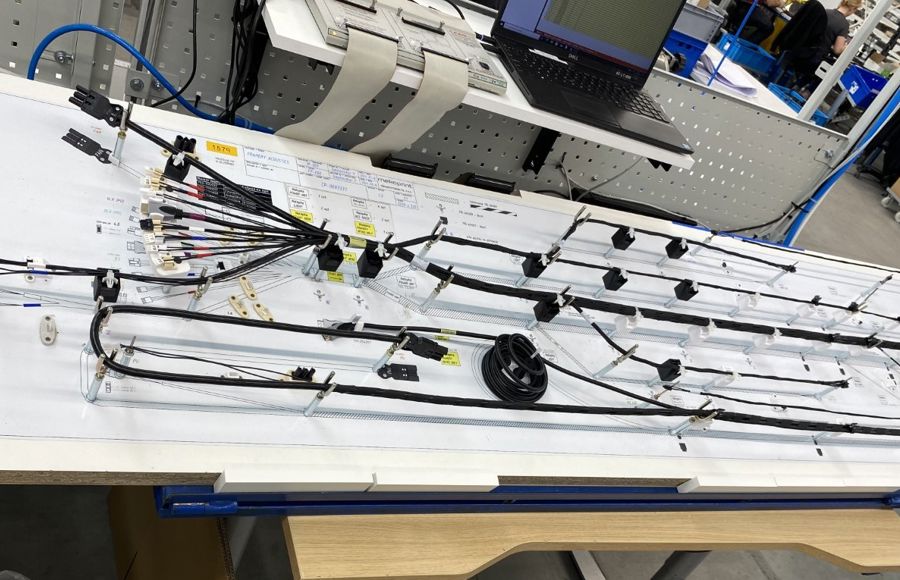
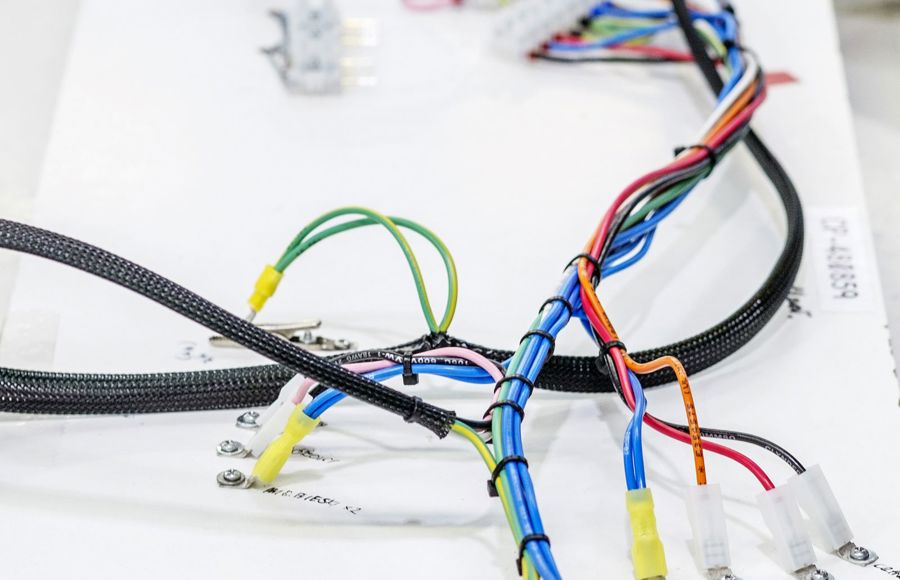
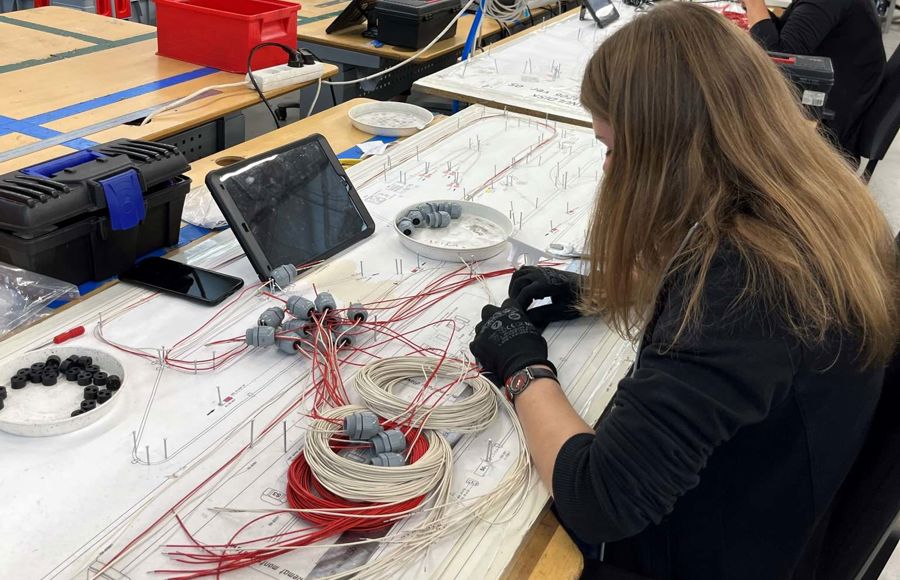
Production equipment available
-
Schleuninger
CSM9100
<6mm2
Komax
Kappa 235
<35mm2
Kinsing
KS-W001
<50mm2
Ramatech
Speedy 35
<185mm2
Ramatech
Speedy 40H
<400mm2
Schleuninger
PS9500RSL
<16MM2
-
Komaxx
Gamma 255
AWG32-AWG14
Komax
Gamma 333PC
AWF24-AWG10
Komax
Alpha 356&565
AWG24-AWG10
KMI
5T5
AWG24-AWG10
Zoko
Zoko-601
Up to 11x AWG18
-
Yuanhan
CJK075
AWG2B-20
-
Hitachi
UXH000071102 OD1,0-16mm
-
Mecal
TT & P100
<6mm2
Mecal
P100&P107
<6mm2
GLW
EC65
<35mm2
Z+F
SC05
<6mm2
Molex
Picoflex
Flat cable
-
Wirmec
SC21
<4,0mm2
Changzhou
HC-2BT+D
<2,0mm2
-
Wiremac
WSC36
<4,0mm2
-
Komax
Mira230&340
Max od 6,4mm
Komax
Mira440
Max od 8mm
Beri
AM ALL AROUND
Max od 25mm
-
ENGBERTS
ICAT
CableEye
Hipot
Hi-pot-215DV tester
CableEye
M2U&M3Z
Up to 1024 connections
KEYSIGHT
P9375A
300kHZ-26,5GHz
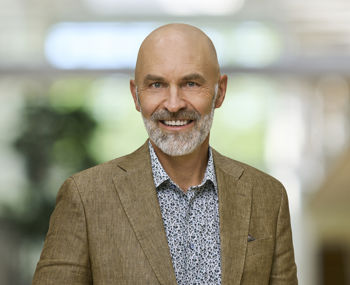
Get in touch with us
Differences between cable assemblies and wire harnesses
What makes cables assemblies and wire harness different is the complexity of their structure. Cable assemblies generally consist of point-to-point, one-pin connector cables sometimes including loop-backs or multiple feet but without complicated layouts.
Wire harness is a product that allows for the simple assembly of big, multidimensional wiring systems. These are mainly known by complex wire and cable arrangements. These solutions are useful when multiple cables are needed for installation which is problematic.
Wire harness design
In general a wire harness is designed to reduce the production cost for a larger component and is based on a specific geometrical and electrical requirement. A wire harness is incorporated to simplify assembly of these large components and integrates them into one or several units to provide a “drop-in” installation.
Sparring on your project?
Please reach out to us for sparring on your new or existing project - We know that early engagement facilitates a more efficient design for manufacturing, substantially impacting the cost-effectiveness of the product through optimised tooling, process capabilities, and material consumption for production.
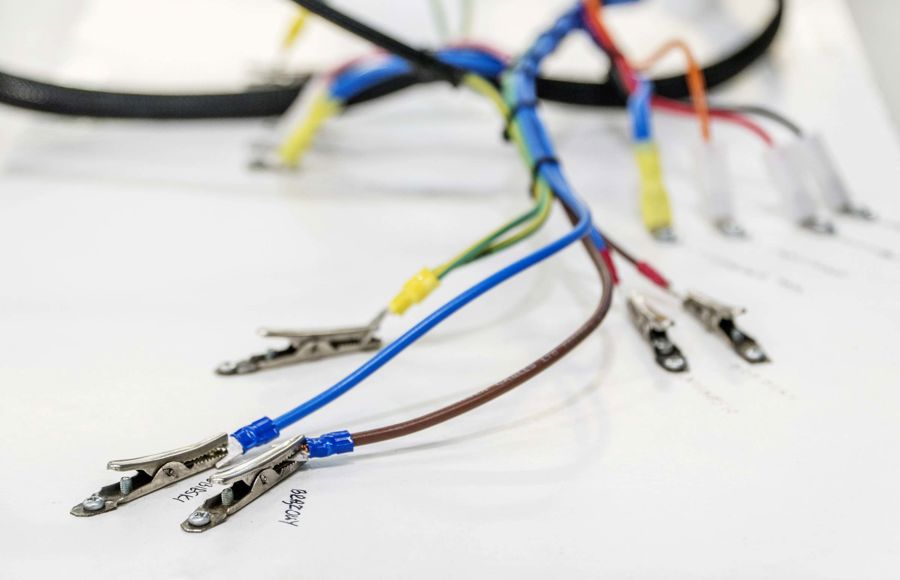
Strong connections
-
Quality testing is a critical part of the wire harness manufacturing process. Samples and prototypes are produced and tested to confirm cable design and construction, manufacturing process, and performance of the cables.
Our production and testing facilities allow for rapid iteration, problem identification, and design refinement to enhance functionality and usability.
-
Our commitment to excellence is backed by ISO 9001, 14001, and 45001 certifications, as well as compliance with IPC/WHMA-620 standards. With a dedicated in-house certified trainer, our team stays updated with the latest techniques, ensuring precision in every custom wire harness we produce.
-
As a trusted partner in wire harness production, we provide full documentation upon request, including Production Part Approval Process (PPAP), First Article Inspection Report (FAIR), and Part Submission Warrant (PSW).
Looking for a reliable partner for your wire harness and cable assembly needs? Contact us today to discuss how we can support your project!
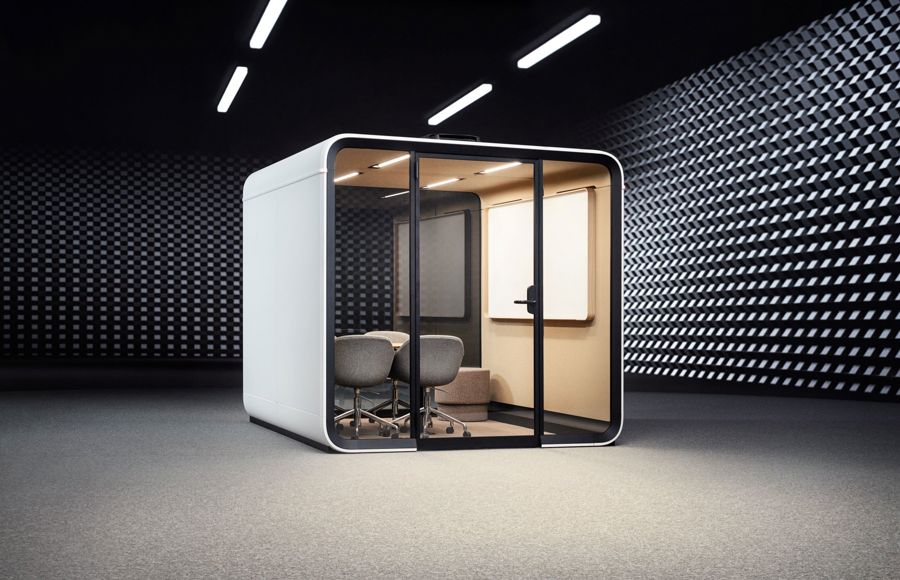
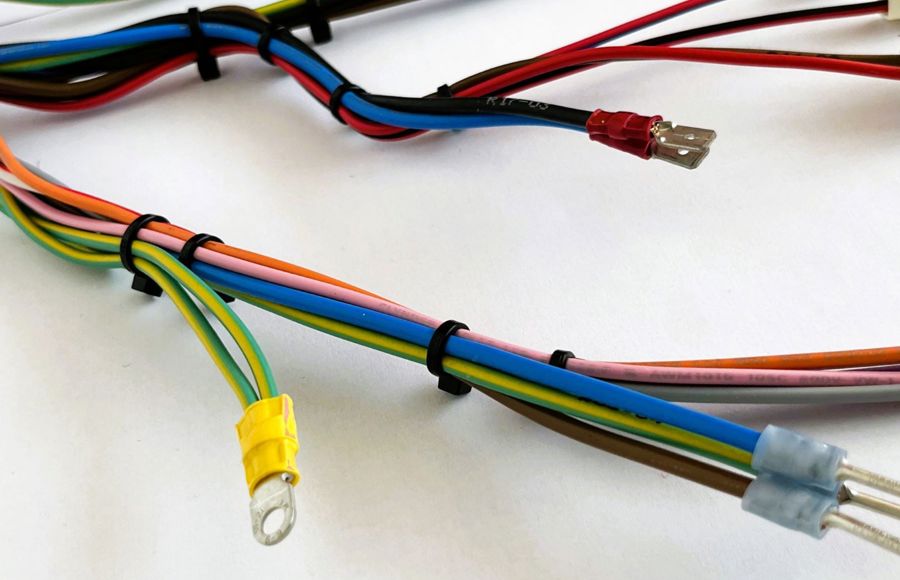
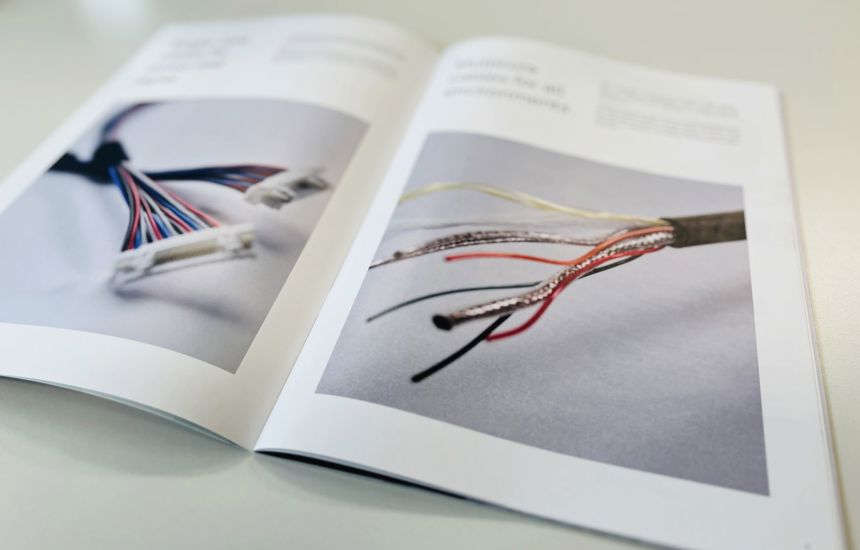
Download free lookbook
-
Multiple insulated conductors bundled together in a single cable structure for enhanced space-saving and efficiency.Multicore cables
-
Molded connectors, housings, or overmolds ensure optimal performance and durability in various environments.Molded cables
-
Single conductors of copper or aluminium, encased in a protective insulation layer, w/o terminals and labelling.Single core cables
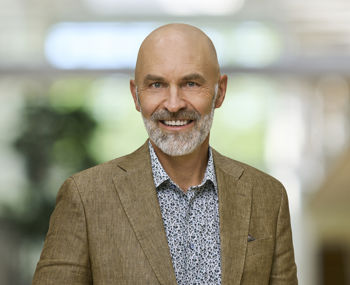