Screen print technique
-
In contemporary screen printing, silk has been replaced by more durable materials like polyester or metal mesh, and the wooden frames replaced with metal frames.
A thick, light-sensitive emulsion is applied to the frames (or screens) to form the precise image to be printed. This emulsion acts as a barrier, ensuring that ink passes through only the designated areas of the fabric, thus creating the intended pattern.
-
A key feature of screen printing is the creation of designs through layers. Each layer corresponds to a graphic color, conductive ink, or lacquer in the final design and requires its own unique screen.
This approach allows for intricate designs and vibrant colors, making each print truly unique.
-
The choice of screen material is critical and is carefully chosen based on the specific needs of the sensor being printed. Factors like the level of detail in the design and the thickness of the ink layers are taken into account.
Screen print at Mekoprint
-
With five multi-station roll-to-roll printing lines, Mekoprint has the daily capacity to produce up to 40 kilometers of sensors and circuits, making us a leader in the industry for high-volume, high-quality printed electronics.
Our production is fully automated with roll-to-roll processes. This automation allows us to handle:
- Single and double-sided printing
- 1, 2, and 3 section printing
-
Our screen printing setup is equipped to handle rolls of sizes up to 750 mm in width and lengths ranging from 250 meters to several kilometers.
- Roll width: up to 750 mm
- Roll lengths: from 250 meters to several kilometers.
- Material thicknesses: from 50 to 500 μm
- Line widths and spacing: down to 50 μm
-
The substrate properties are of significant importance when using printed electronics as a key components. The substrates used in our production are thin, lightweight, flexible, or stretchable
- Polyester (PET)
- Polycarbonate (PC)
- Polyethylene Naphthalate (PEN)
- Non-woven materials
- TPU foil
-
The choice of inks are based on the needed level of functionality, quality, and price. You may benefit from a number of already tested and proven inks, or we may investigate new inks to fit your specific application.
- Conductive ink: silver, carbon, PEDOT
- Graphic inks
- Dielectric ink
- Lacquers
- Etch resist
- Solder mask
Custom roll-to-roll finishing at Mekoprint
For us, your production efficiency is our priority. We ensure that every product delivered is not only functional but also perfectly suited to your subsequent manufacturing environment to maintain a smooth and efficient workflow.
We offer a range of finishing techniques tailored to complete the printed component. Whether you need precise cutting, embossing, lamination, or comprehensive testing, our roll-to-roll processes are designed to deliver high-quality results with minimal manual handling.
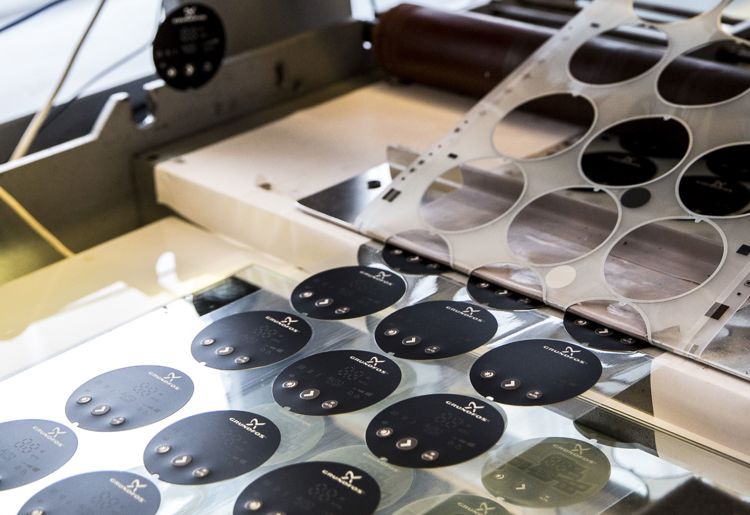
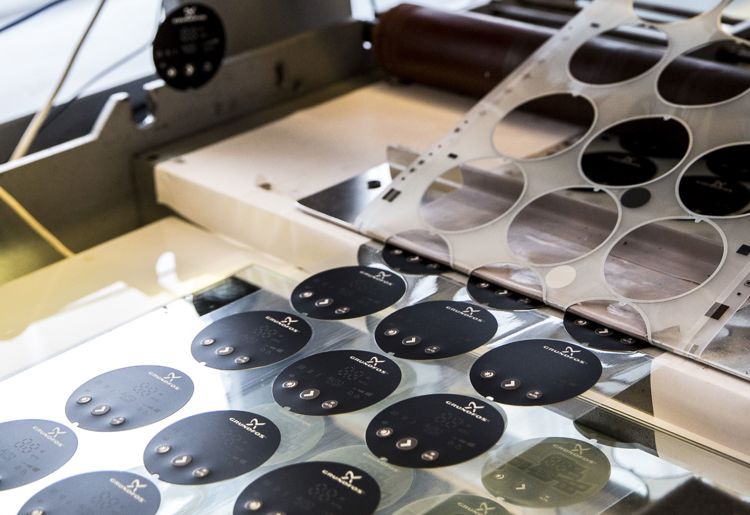
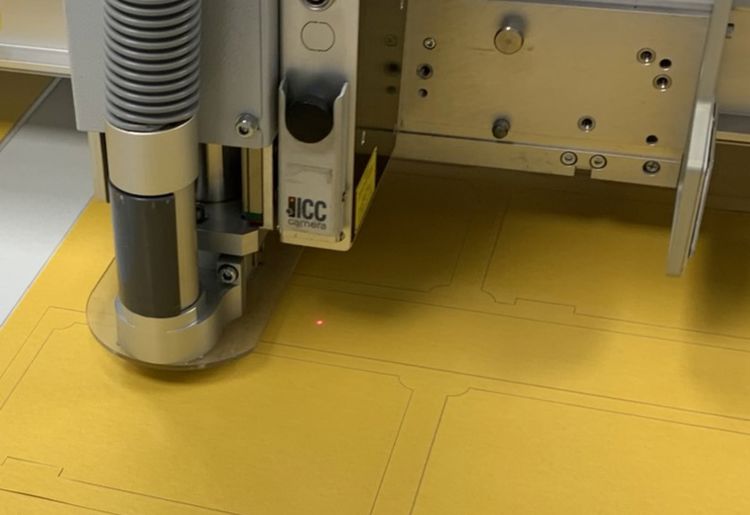


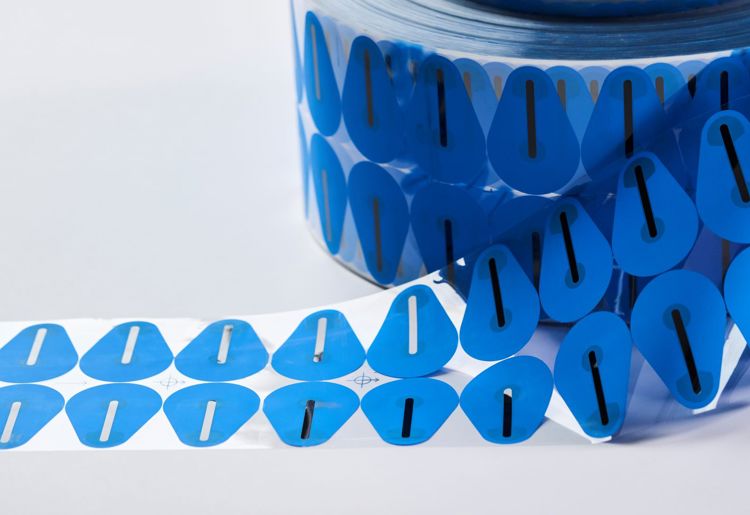
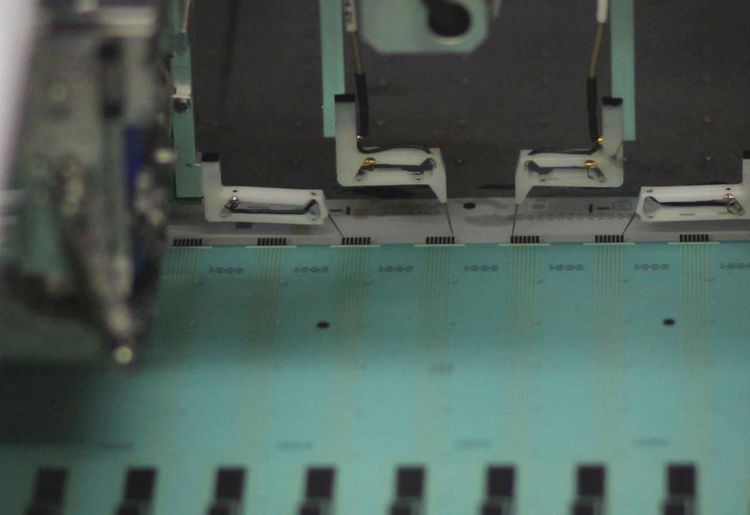
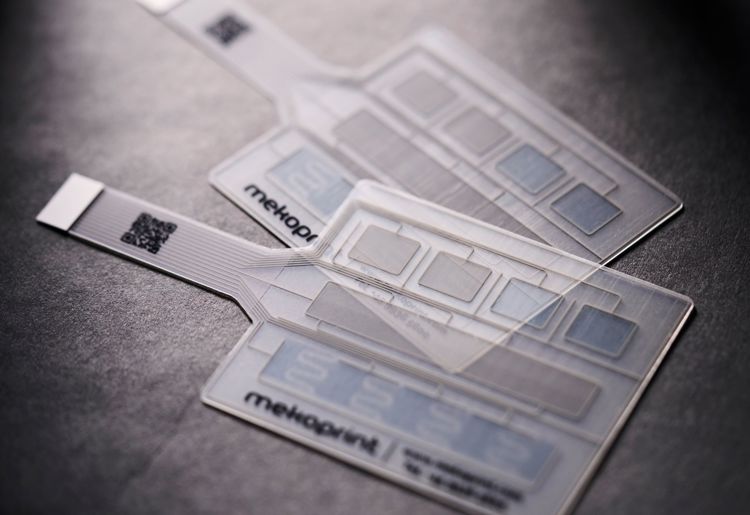
-
Die cutting efficiently shapes sensors directly from the material, including kiss-cut down to the adhesive liner, simplifying the removal of excess material.
This process benefits from minimal manual handling. With camera-controlled precision and periodic digital measurements checks ensures accuracy.
Depending on the project's needs and tolerances, we customise tooling materials to optimise cost and meet stringent specifications.
Integrated processing options such as lamination, embossing, and slitting may be combined in a single production pass for efficiency.
-
Laser cutting offers a high level of precision, perfect for creating fine contours that are hard to achieve with traditional die-cutting.
Suitable for both high-speed roll-to-roll production and table laser tasks. We choose the method that is best adjusts to the size of production batch and specific material requirements.
For smaller production runs, laser cutting is cost-effective as it eliminates the need for additional tooling investments.
-
Our embossing process adds depth and texture to materials, enhancing both aesthetics and functionality to an otherwise smooth surface.
This technique can apply a 3D effect across the entire surface or focus on specific features such as borders, buttons, or logos.
Custom embossing is available, including tactile features like Braille, to meet diverse design requirements.
-
Lamination protects and enhances the durability of printed sensors by bonding them with other layers, such as other substrate foils, protective overlays, or adhesives.
Our precise, camera-monitored lamination process ensures alignment and adherence to strict tolerances, maintaining high quality even with minimal manual handling.
-
We tailor the width of large rolls to your specific needs. Ensuring easy handling and integration into further processes - whether in our production or yours.
-
We have invested in cutting-edge technology for automatic electrical function testing of printed electronics on rolls.
Using advanced flying probe technology, large volumes are handled efficiently. This setup not only offers high accuracy but also keeps startup costs low.
Test specifications are of cause customised your requirements.
-
Finished parts from Mekoprint are prepared and optimised for easy integration into your production lines.
Delivered either stamped to size, cut into sheets, or on rolls suitable for automatic pick-and-place. We make sure they are ready for your immediate use.
-
Cost-efficient, lightweight, and flexible user interfaces in applications where touch operation is preferred.Capacitive touch sensors
-
Ultra-thin wearable sensors ideal for single-use health care applications. Brings electronics close to the body.Wearable sensors
-
Flexible circuits cut down on space and weight. Ideal for devices where a rigid circuit board will be impractical.Flexible circuits
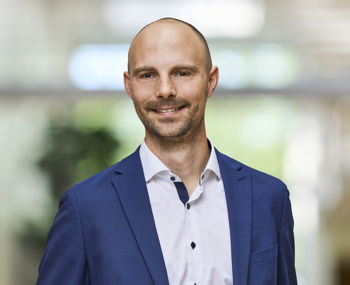