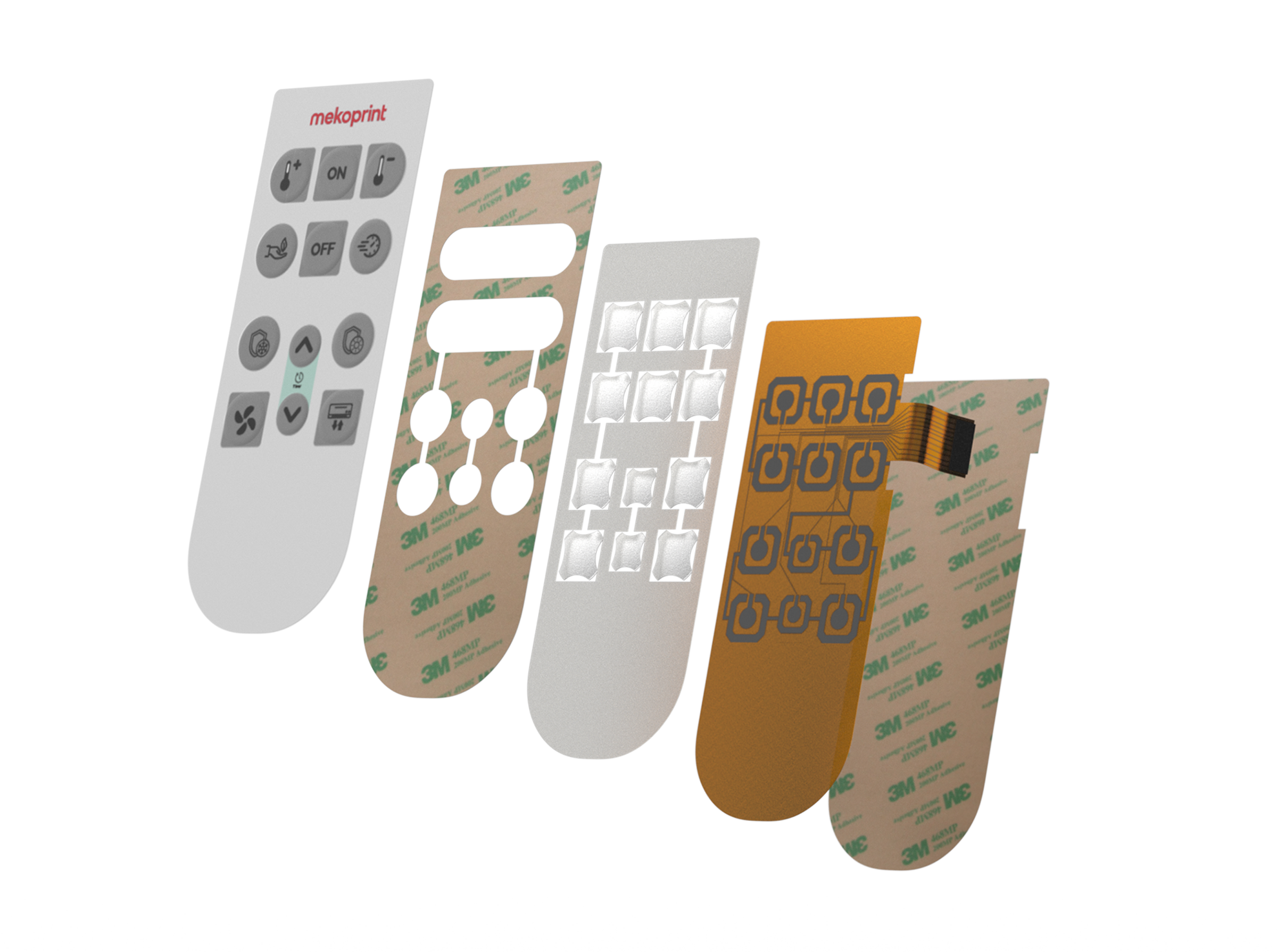
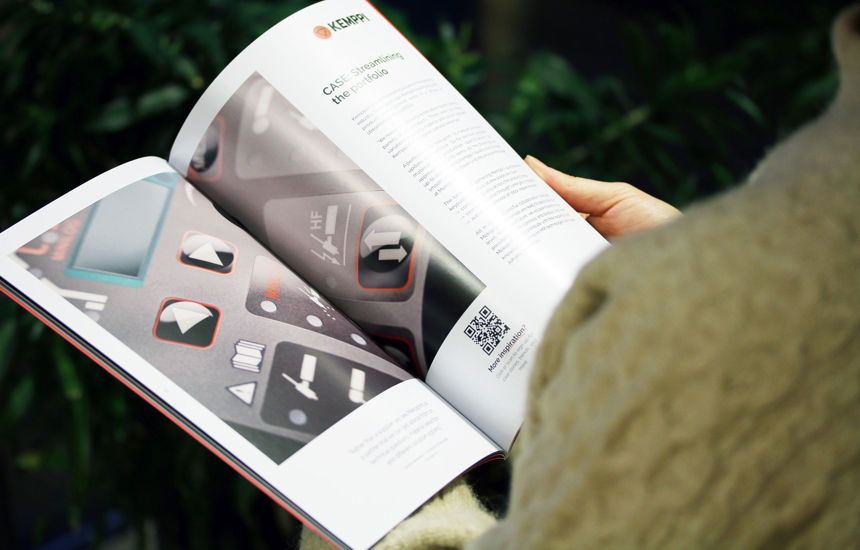
Download HMI lookbook
Applications & environments
Membrane keypads are used across industries including medical devices, industrial electronics, and consumer products. Each solution is engineered to match the environmental demands of the application. This could include IP classification, outdoor UV exposure, daily cleaning, or hygiene requirements in sterile environments.
Material selection & durability
The choice of materials for the front film and inner layers has a direct impact on quality, durability, functionality and the visual appearance of the keypad. UV-resistant or anti-bacterial finishes may be needed, depending on where and how the product is used. Flame retardant and antistatic properties can also be integrated.
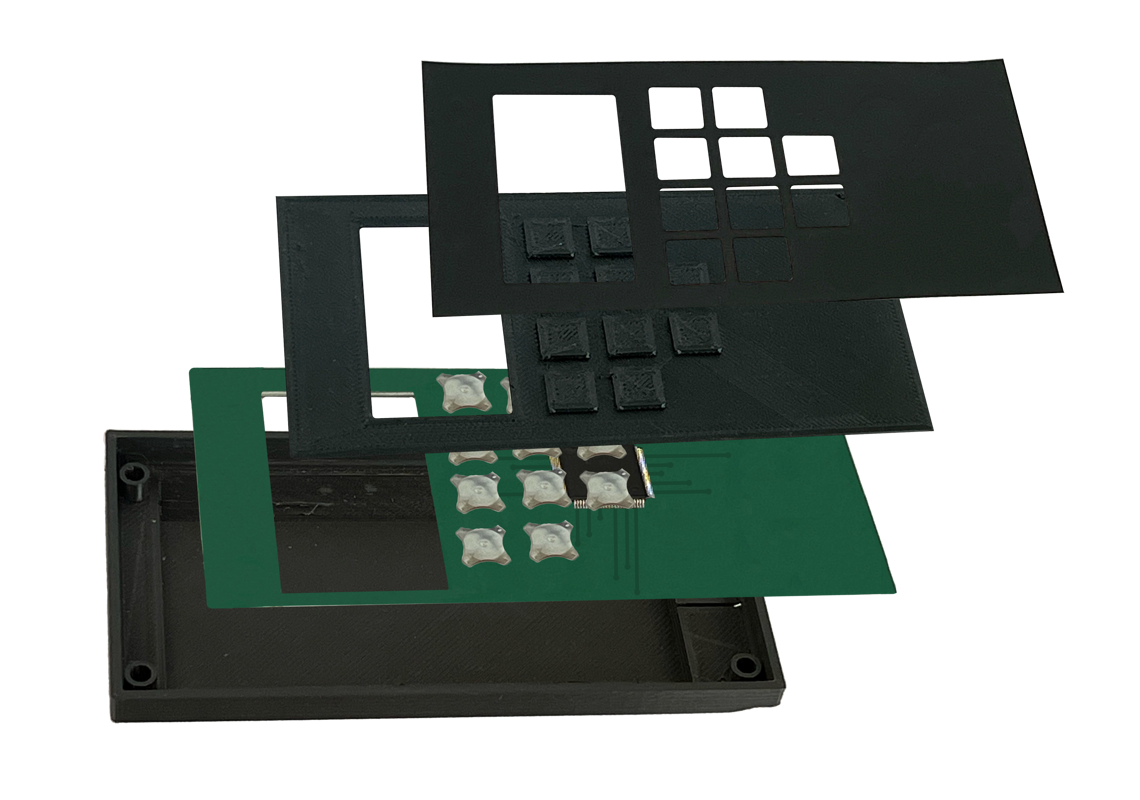
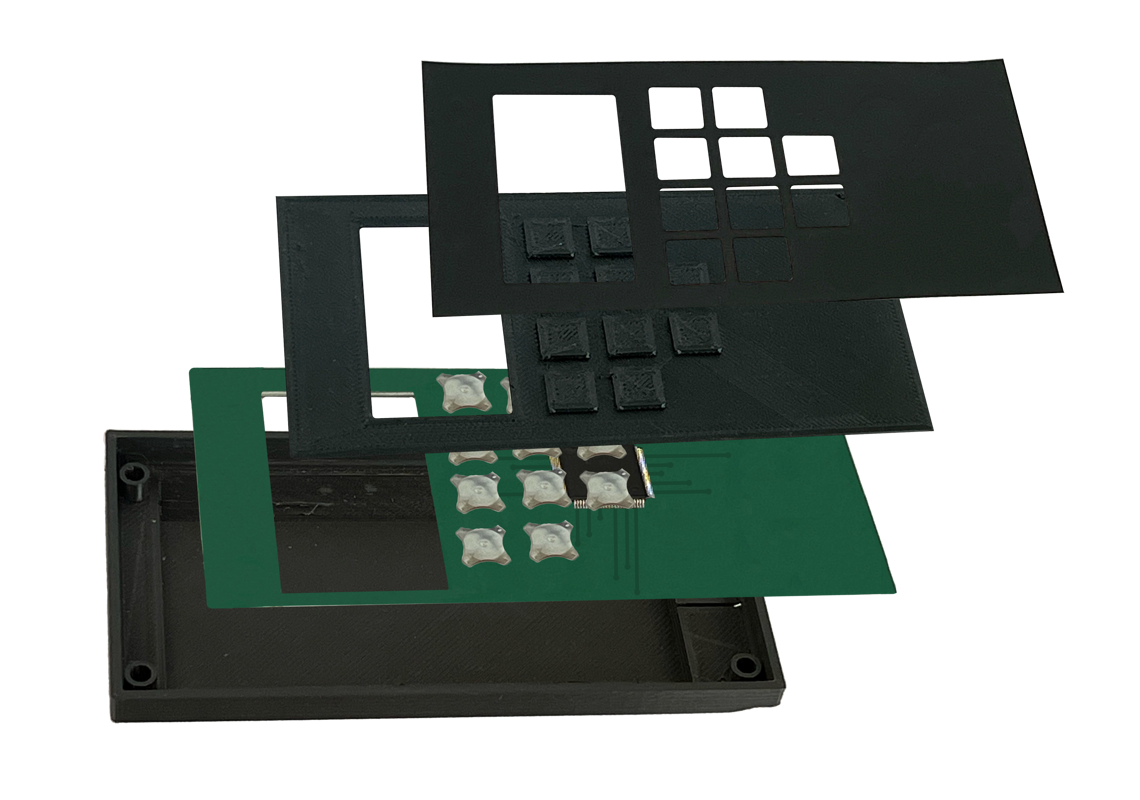
Engineering of a membrane switch keypad
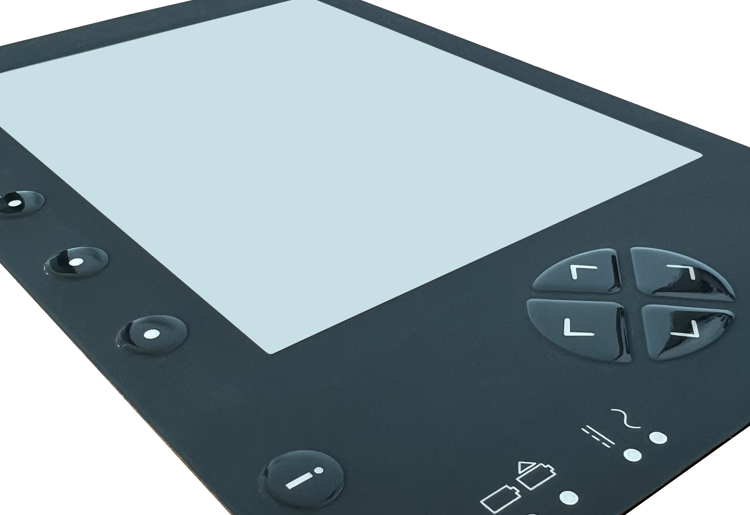
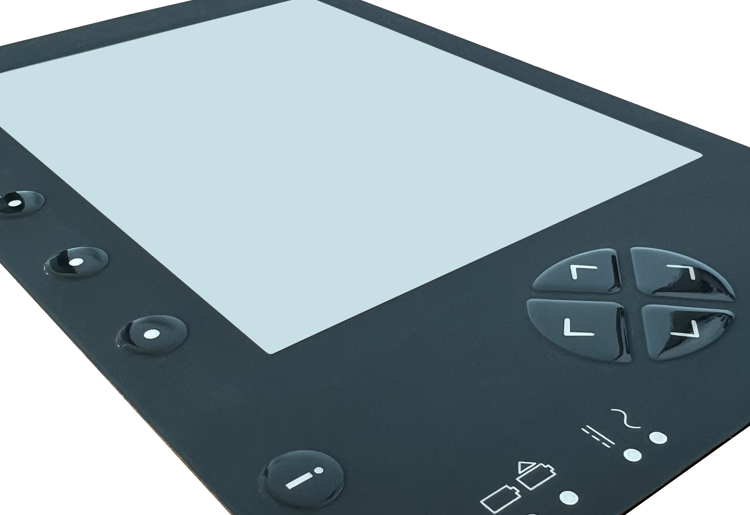
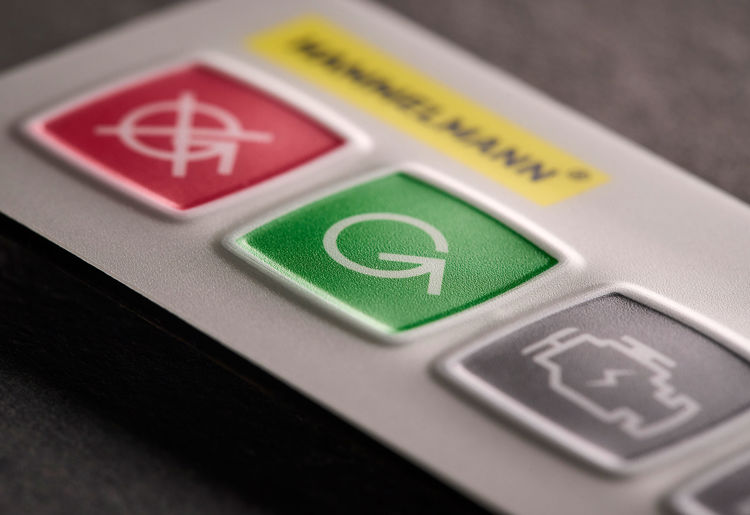
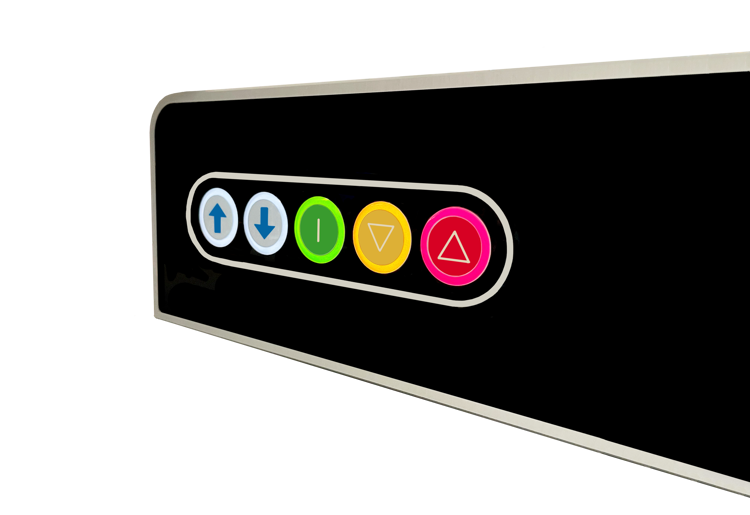
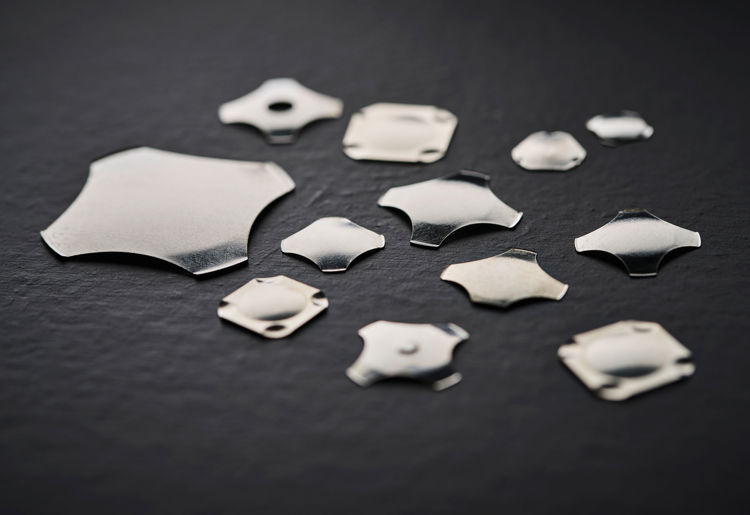
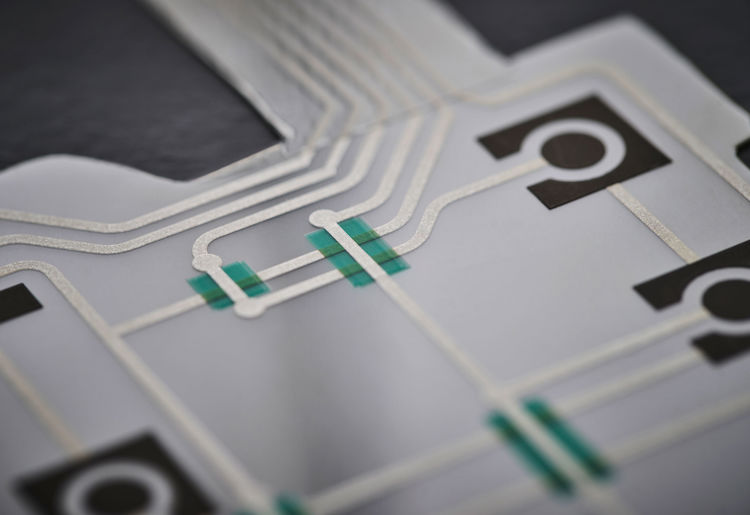
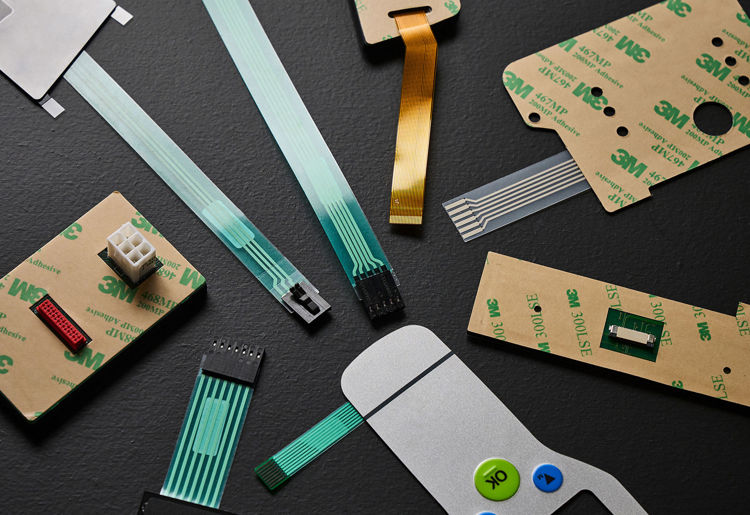
-
The finishing front of a membrane switch plays both a decorative and functional role.
- You can use gloss contrasts to highlight different interaction points on your keypad.
- Gloss can also play an aesthetic role to communicate your product's brand.
- Finish may also be coatings, for example UV resistance coating, or antistatic coating, or flammability protection layer. These are selected based on the usage environment.
-
You can add colour to the top layer of your membrane keypad through screen printing or through digital printing.
- Screen printing on foils and films ensures colour accuracy, UV resistance and abrasion resistance. The technique offers a range of possibilities including metallic colours, translucent details, RAL and PMS colours, light-blocking features, non-conductive inks.
- With digital printing the options are countless. You can achieve photorealistic graphics including gradients and other graphic details.
- Combination of screen and digital printing combines the best of both words, offering highly detailed graphics of digital print and lightproof colours of screen printing.
-
You can use LEDs in many different ways in a membrane switch - for decorative, functional or combined purposes.
- Decorative light features are usually used as dead-front effects or ghost effects where symbols are visible only when lit.
- Backlighting is often used to illuminate all keys for operation in dark environments or at night.
- Status indicators are commonly used with status windows or backlit symbols. LEDs or light guide films (LGF) can be used, and alternating colours may be applied to indicate function or state.
-
The most common way to create a tactile click in a membrane keypad is by using metal domes.
Domes come in many sizes, shapes and actuation forces. The choice of domes is defined by your specifications and your requirements for:
- the tactility - audio and haptic feedback of the key
- lifetime of the HMI solution. - number of activations of a key during the products lifetime
Embossing of keys can also contribute to tactile feedback and visual guidance. Shaped keys or 3D-effect embossing are often used to assist with intuitive operation.
-
The electrical or circuit layer in a membrane keypad is usually made with:
- PET - the most common and cost effective solution
- FPC - copper-based foil with high conductivity and flexibility
- PCB - offering stiffness and possibility for component soldering
The most suitable circuit layer depends on the product's environment and the electrical and mechanical concept. If the keypad includes backlight, the circuit layer design must allow for light transmission and proper insulation.
-
The details about mechanical and electrical integration of a keypad have great impact on the actual keypad solution. Some of the most important questions to consider during the design process:
Mechanical integration:
- How will the keypad be fixed to the product? Adhesive, screws or press-mounting?
- What is the direction of assembly? Front-mounting, back-mounting or side-mounting?
Electrical connection:
- What is the distance from the keypad to the product’s PCB? How long is the connecting tail?
- Will the tail be bent or twisted during installation?
- Are there vibrations or pull on the connection during use?
- Will the keypad be disassembled during service?
Displays, touchscreens or full enclosures can also be integrated. This may involve OCA bonding of displays, FPC/PCB interfaces and precise tolerance control in mechanical parts. Mekoprint offers full assembly and integration support.
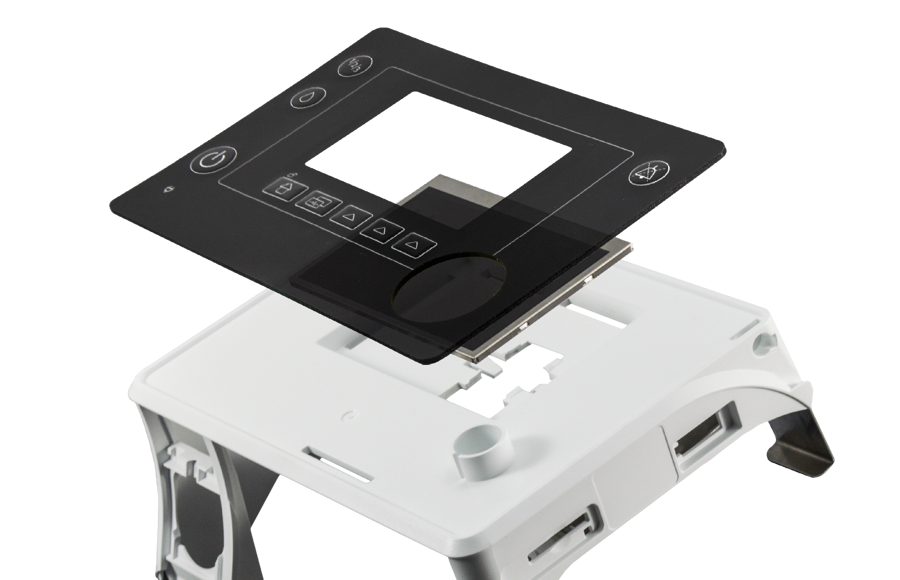
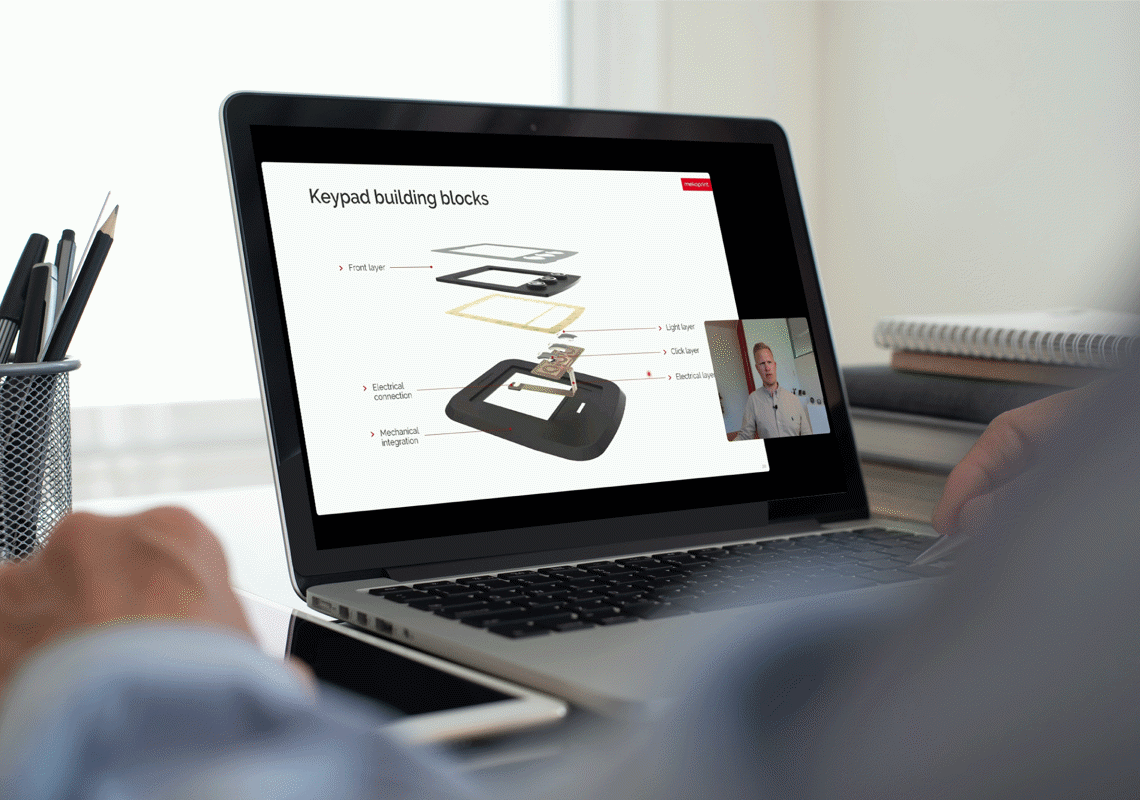
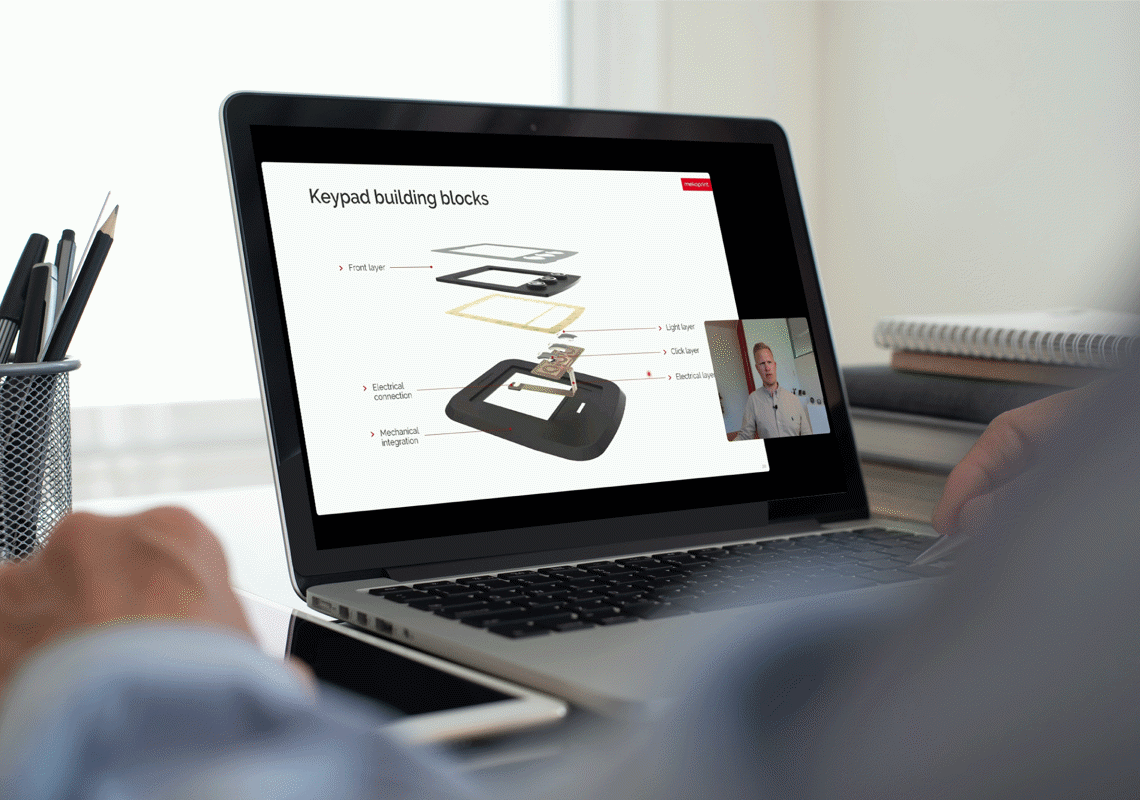
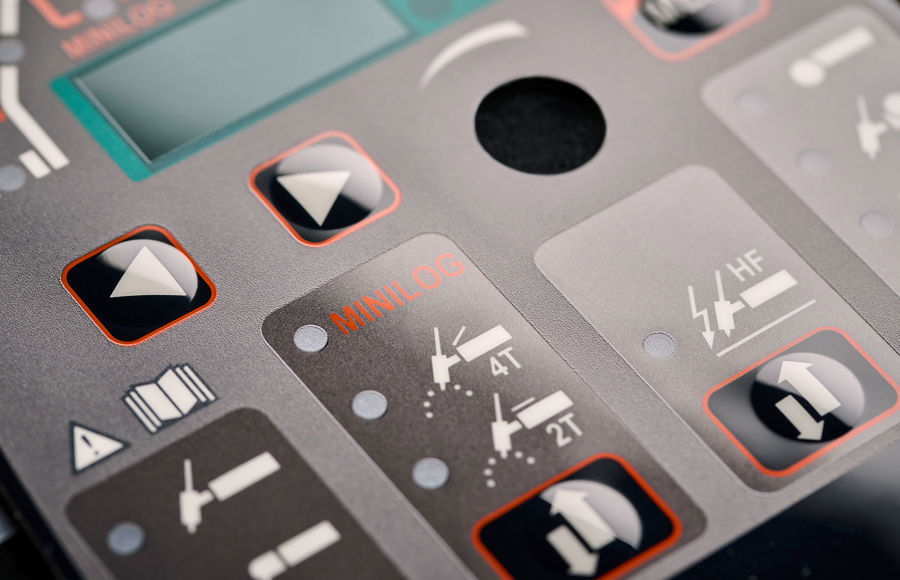

Order a free keypad sample
-
Graphic overlays and front foils as front covers for HMI sections on your productGraphic overlays
-
Silicone keypads with great tactile feedback, sculpted design opportunities and exclusive look & feelSilicone rubber keypads
-
HMI assembly for easy mechanical and electrical integration with your productHMI assembly
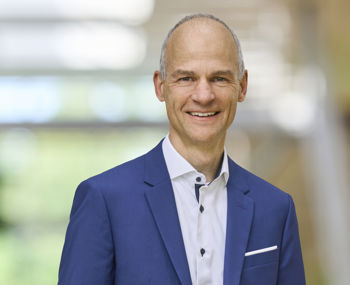