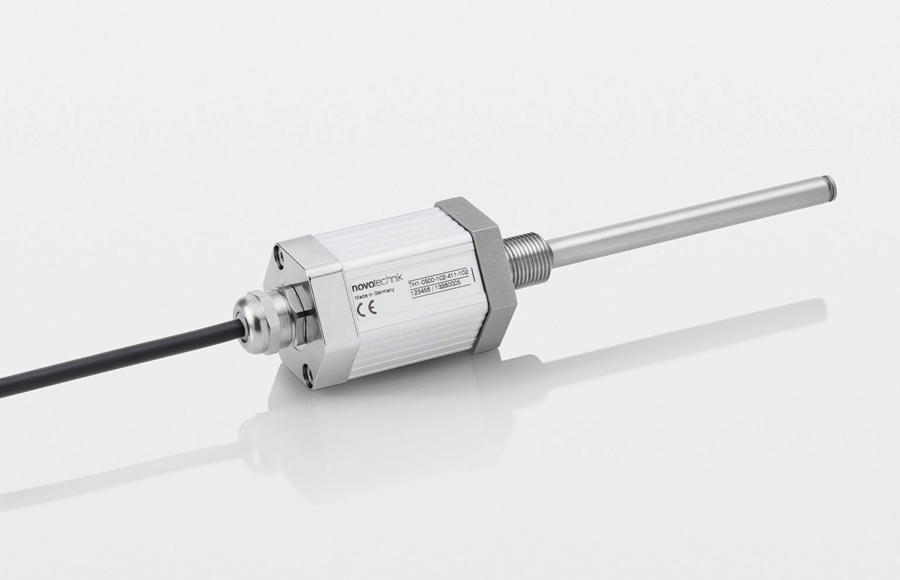
Contact sensors
Contact sensors measure physical movements or positions through direct mechanical interaction, often using components like wipers or sliders. While they are straightforward and cost-effective for many applications, their reliance on physical contact makes them prone to wear and tear over time, especially in environments with dirt, high repetition rates, or contamination
Non contact sensors
In demanding applications, non-contact sensors offer a superior alternative. They measure using a separate position marker, eliminating friction and reducing wear. This makes them more reliable, durable, and suitable for challenging environments, often with a high IP rating for resistance to dust and moisture.
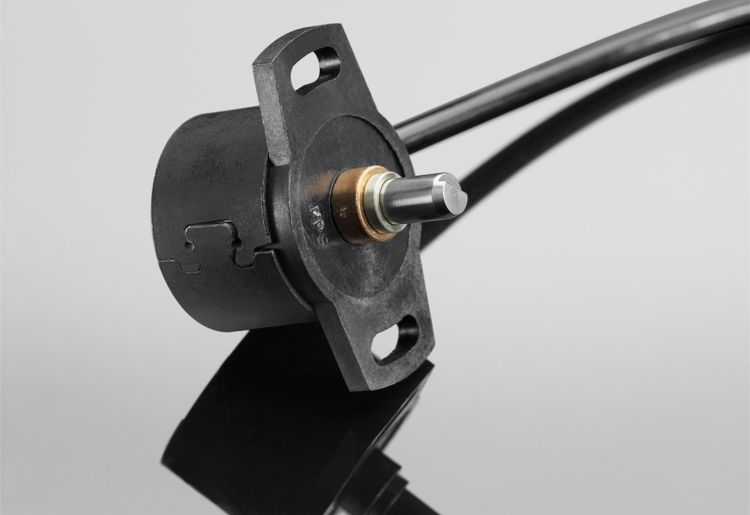
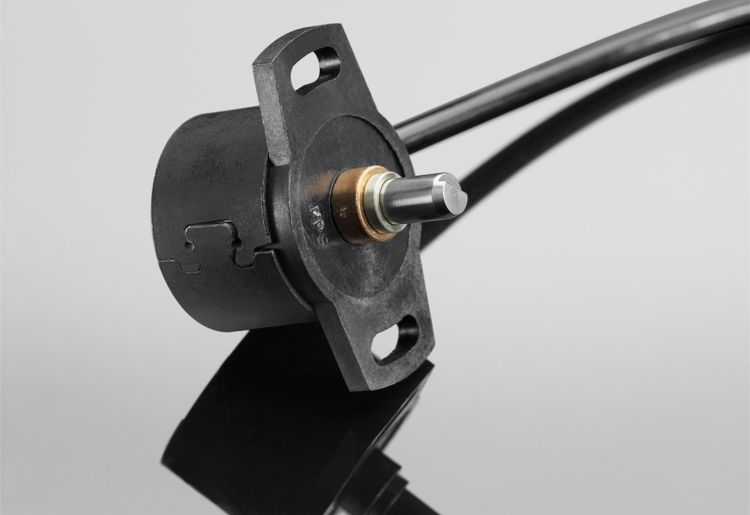
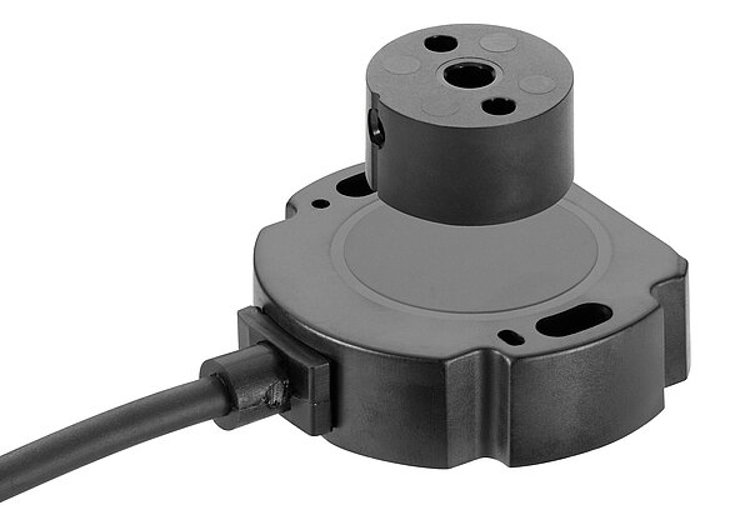
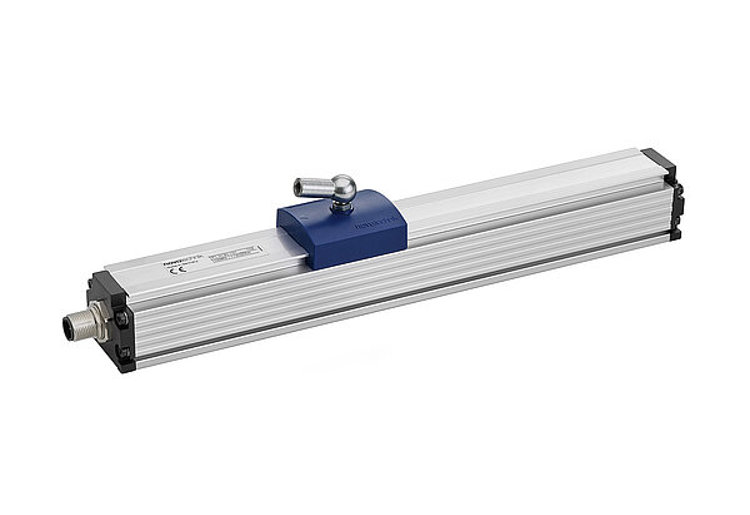
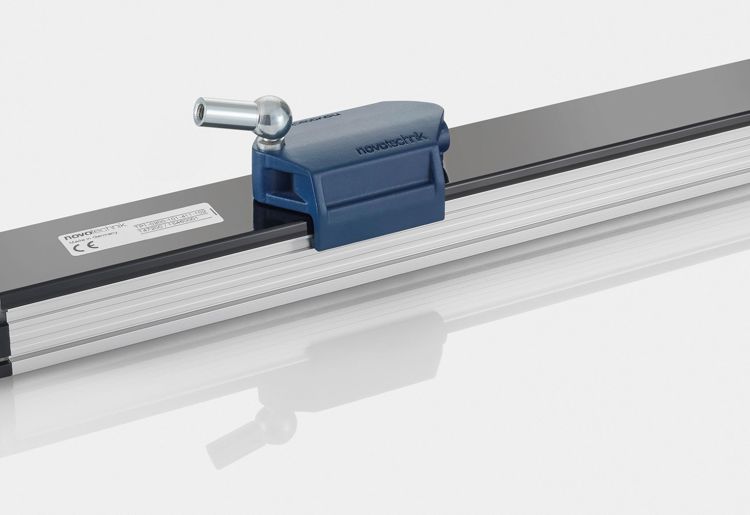
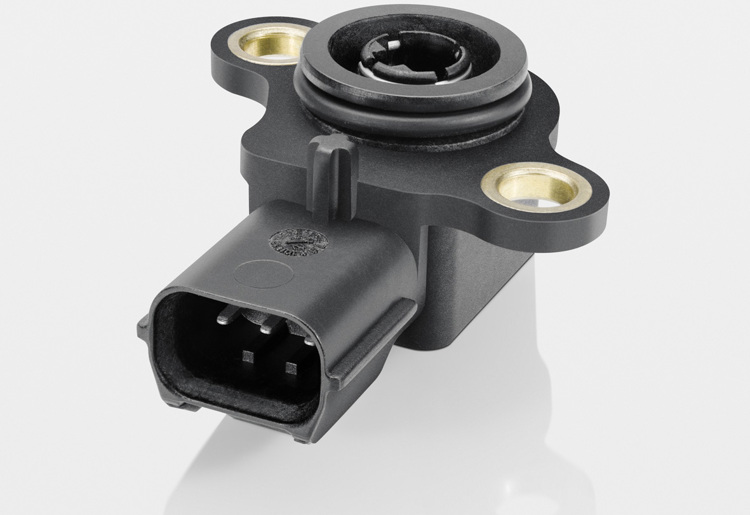
-
Many applications need rotation counters to measure angles beyond 360º. Common low-cost 10-turn potentiometers often fall short in resolution and reliability, while optical absolute encoders are too expensive for many uses.
Optical encoders also need continuous power, losing their count when power is interrupted. Geared rotation counters, on the other hand, can wear out over time.
Novotechnik’s 2800 Series multi-turn rotary sensors provide a practical solution. These sensors use patented NOVOTURN™ technology, based on an advanced giant magnetic resistance effect. They are more cost-effective than optical encoders, maintain high reliability and accuracy, and include additional useful features to meet user needs.
-
-
Magnetostriction is the elastic deformation of ferromagnetic materials like iron, nickel, and cobalt during changes in magnetization. This occurs due to shifts in the alignment of magnetic regions called Weiss domains. When exposed to an external magnetic field, some domains align, causing mechanical deformation and generating a torsion wave that travels at 2,800 m/s.
A magnetostrictive waveguide is housed along the measuring path, with position marked by an external magnetic field. A short current pulse interacts with this field, creating a torsion wave. The wave's travel time to a converter is measured and processed into a precise position value, offering a reliable and contact-free measurement solution.
-
Non-contact sensors are increasingly needed for harsh environments with dynamic movements and high contamination levels. They offer long service life, even under mechanical stress, and are durable at high speeds and frequencies where potentiometers would wear out.
These sensors provide standardised electrical interfaces, low power consumption (typically <100mA), and remain cost-effective, making them ideal for demanding applications like engines and agricultural machinery.
-
Advancements in control engineering, microprocessors, and semiconductor technology have led to the widespread adoption of electronically controlled systems across industries. This has driven demand for sensors that are both cost-effective and durable, capable of withstanding extreme temperatures (e.g., -40 to +160°C). These sensors are particularly critical in high-volume applications like the automotive industry.
Interfaces
-
- Multi-master system with distributed network management.
- Capable of supporting up to 254 logical nodes.
- Data is organized as parameters (signals) grouped into parameter groups (PGs) across four memory pages (data pages).
- Each parameter group is uniquely identified by a Parameter Group Number (PGN).
-
- Wide variety of methods available for configuring bus device parameters.
- Includes error detection and handling mechanisms.
- Device data is accessible through electronic data sheets (EDS files).
- Additional functionalities include cam switches, limit value switches, and speed data.
- CANopen is ideal for use as an interface in dynamic applications and complex control networks.
-
- Reliable fail-safe digital communication at the sensor level.
- Cost-effective installation using unshielded 4-pole cables.
- Seamless integration with existing Ethernet-based or fieldbus communication systems.
- Supports condition monitoring and predictive maintenance.
-
-
- Digital interface for absolute position and rotary measuring systems, ideal for industrial environments.
- Transmits position data synchronously with the controller via RS 422, using 24- or 25-bit binary or Gray-coded formats.
- Optional parity bit ("SSI26") for enhanced data security.
- Clock frequencies range from 60 kHz to 2 MHz, with update rates up to 16 kHz.
- Reliable, dynamic, and cost-effective, with performance dependent on cable length and driver blocks.
-
Single conductors of copper or aluminium, encased in a protective insulation layer, w/o terminals and labelling.Single core cables
-
Multiple insulated conductors bundled together in a single cable structure for enhanced space-saving and efficiency.Multicore cables
-
Molded connectors, housings, or overmolds ensure optimal performance and durability in various environments.Molded cables
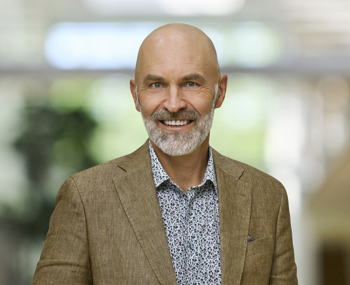