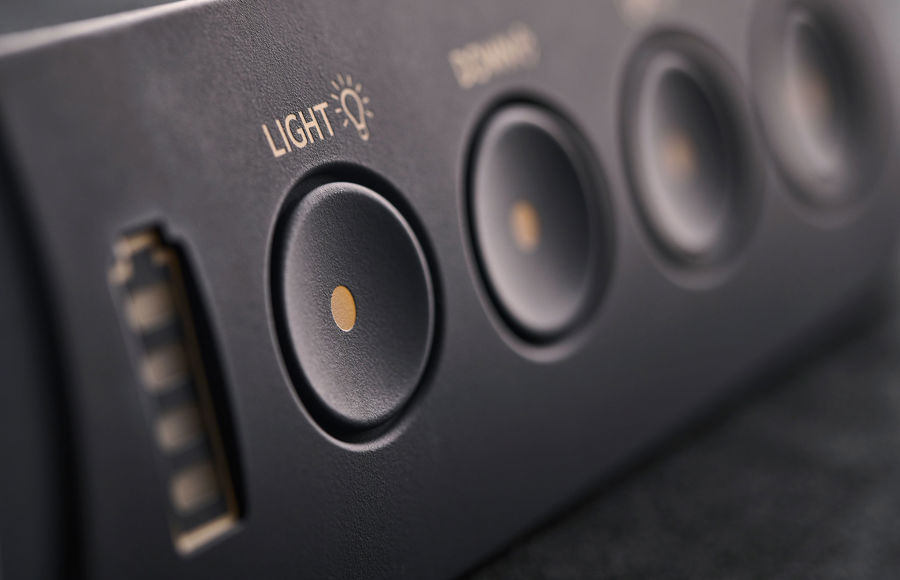
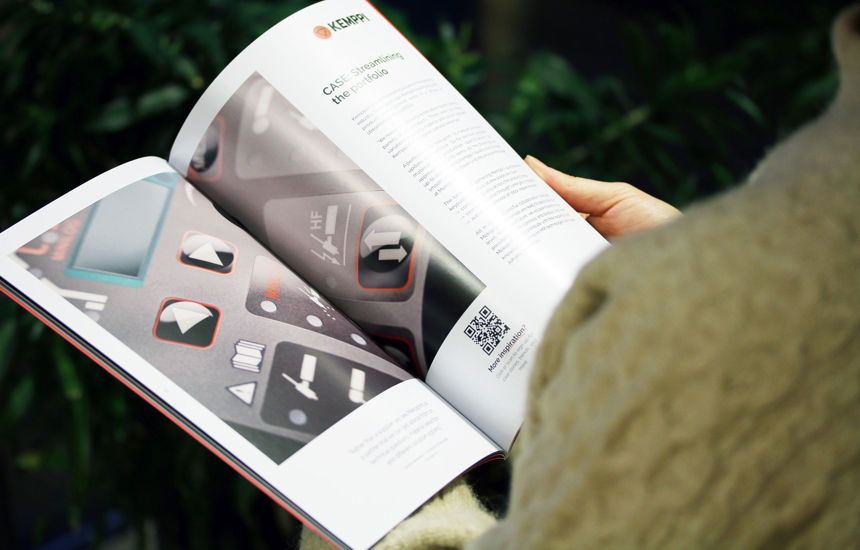
Download HMI lookbook
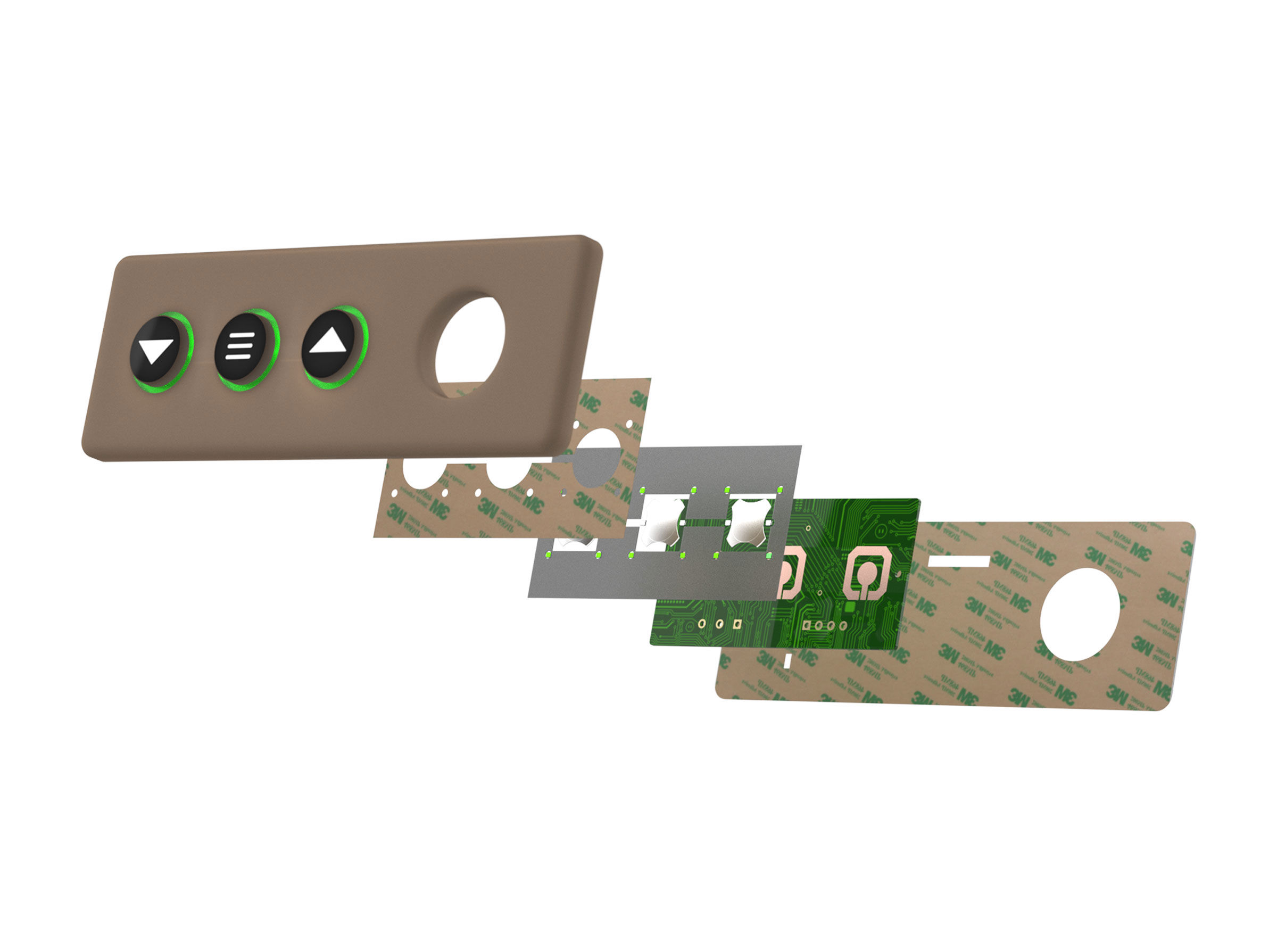
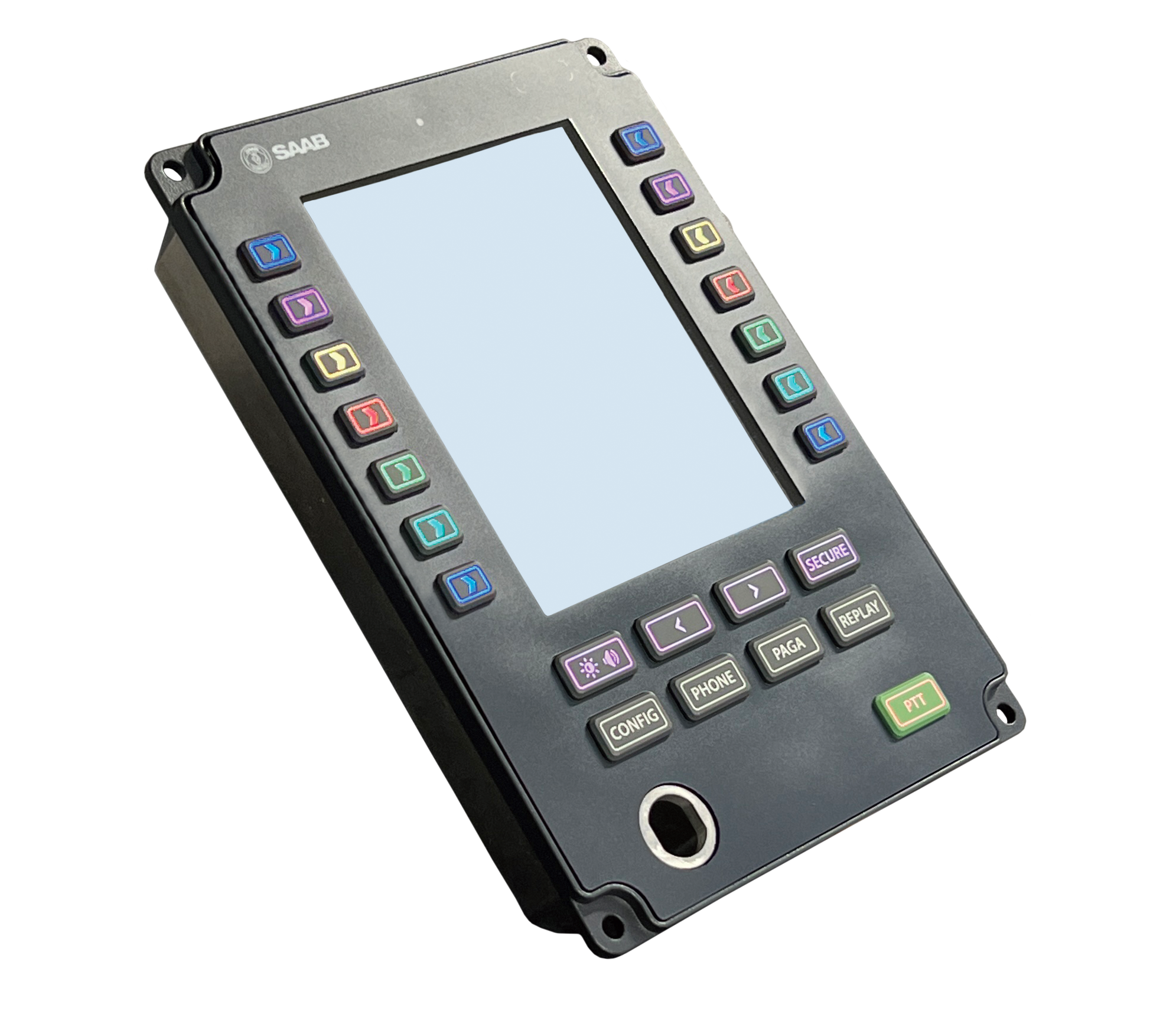
Applications across industries
Silicone rubber keypads are widely used switch technology in the electronic industry. Silicone keypads are integrated in devices in industrial and professional environments where durability, precision, and environmental resistance are critical. These keypads offer rugged reliability in sectors that demand high-performance human-machine interfaces.
User-friendly in gloves and challenging conditions: The silicone keypad’s firm tactility and customisable surface structure ensure reliable operation—even when used with gloves. Raised key profiles, tactile feedback and clear separation between buttons make it easy to operate equipment where precision and speed are critical, such as in emergency care, industrial machinery or remote field work.
Industrial automation and heavy machinery: In factories, processing plants, and heavy equipment, silicone rubber keypads serve as control panel interfaces, machine operation consoles, and safety system inputs. Their abrasion resistance and chemical resistance make them ideal for harsh industrial environments where exposure to oil, grease, and solvents is common. With backlighting, these keypads remain visible in dimly lit control rooms or outdoor sites.
Agriculture & construction equipment: Modern tractors, harvesting machines, and earthmoving equipment rely on rugged keypads for operator controls. These keypads withstand dust, moisture, and temperature extremes, ensuring seamless functionality even in outdoor or high-vibration environments.
Medical & laboratory equipment: In hospitals, diagnostic labs, and surgical environments, silicone rubber keypads are used in patient monitoring devices, imaging systems, and sterilization equipment. Their chemical resistance ensures they can be regularly cleaned and disinfected without degradation. With customizable tactile feel and actuation force, they provide reliable input for precision-sensitive devices.
Communication & safety equipment: From two-way radios to emergency response systems, personal communication devices rely on membrane keypads for critical input functions. Silicone keypads are designed to withstand shock, water exposure, and constant use, making them ideal for military, security, and emergency service applications.

Business Development Manager, Mekoprint
Domenic Breitbart Nielsen
Design and customisation options
At Mekoprint, we specialize in crafting silicone rubber keypads that seamlessly integrate with your product's design and functionality. Our comprehensive customization options ensure that each keypad not only meets your technical requirements but also enhances the overall user experience.
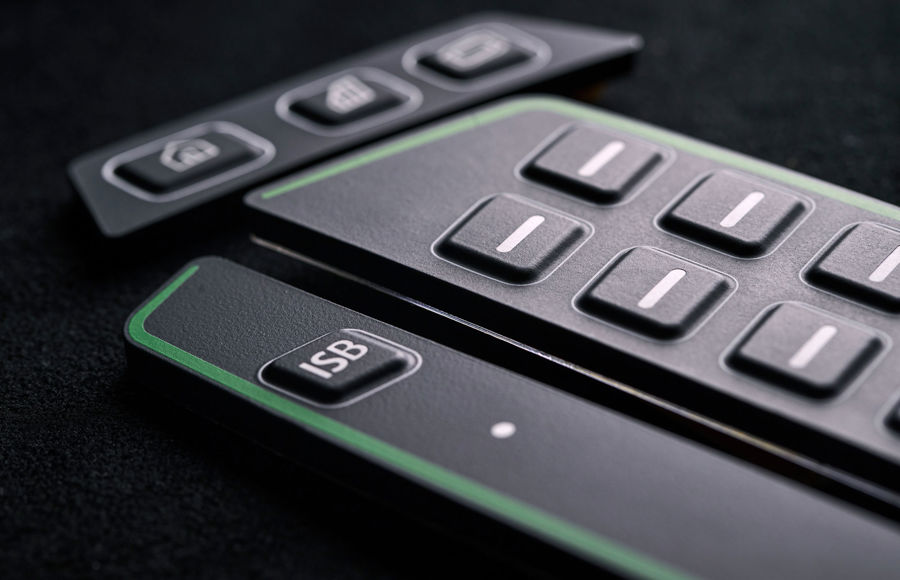
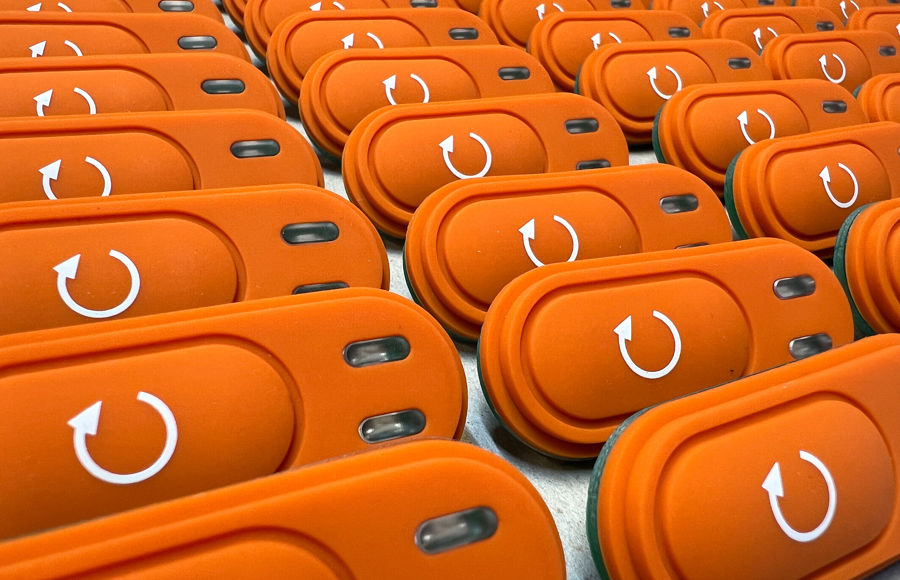
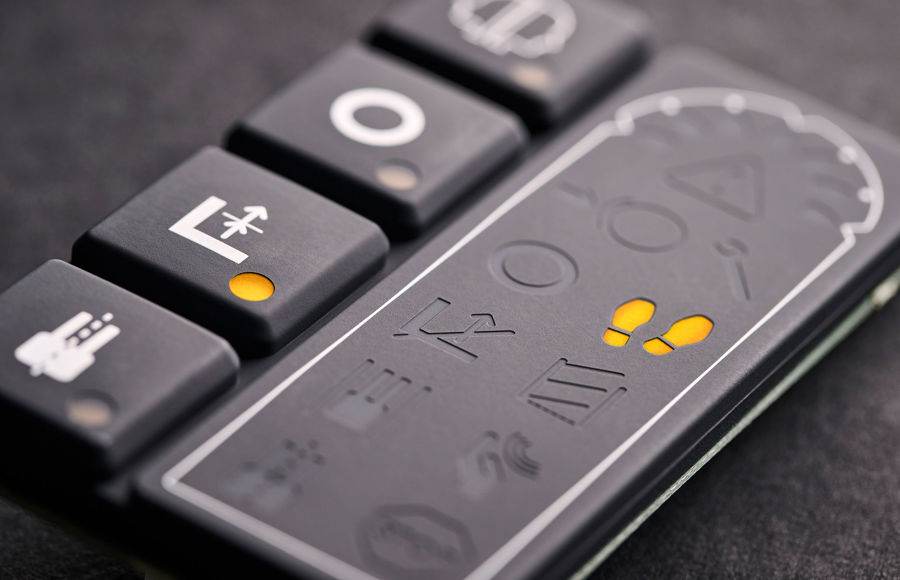
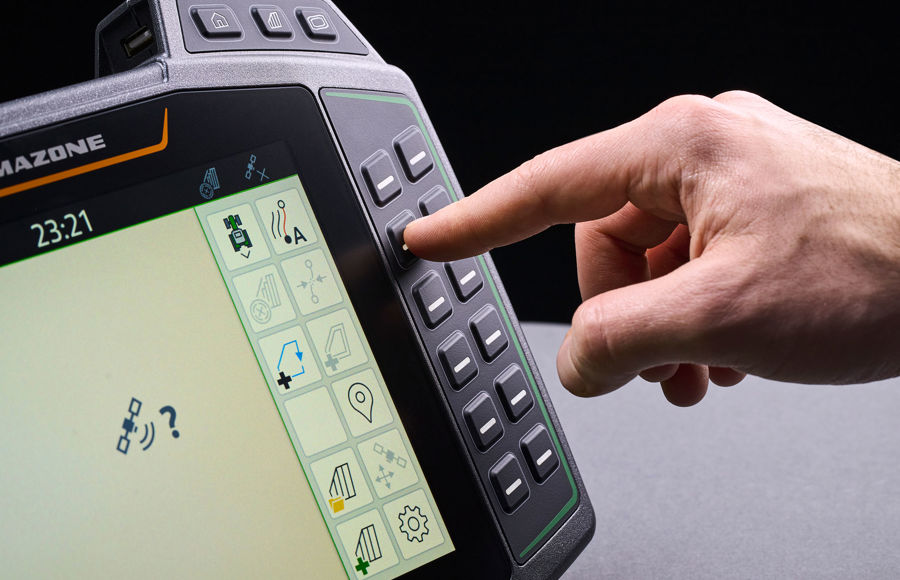
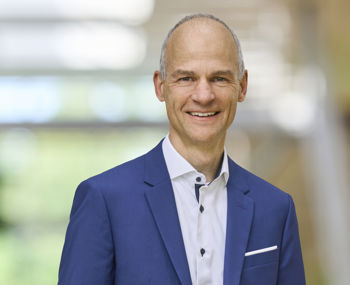
Get in touch with us
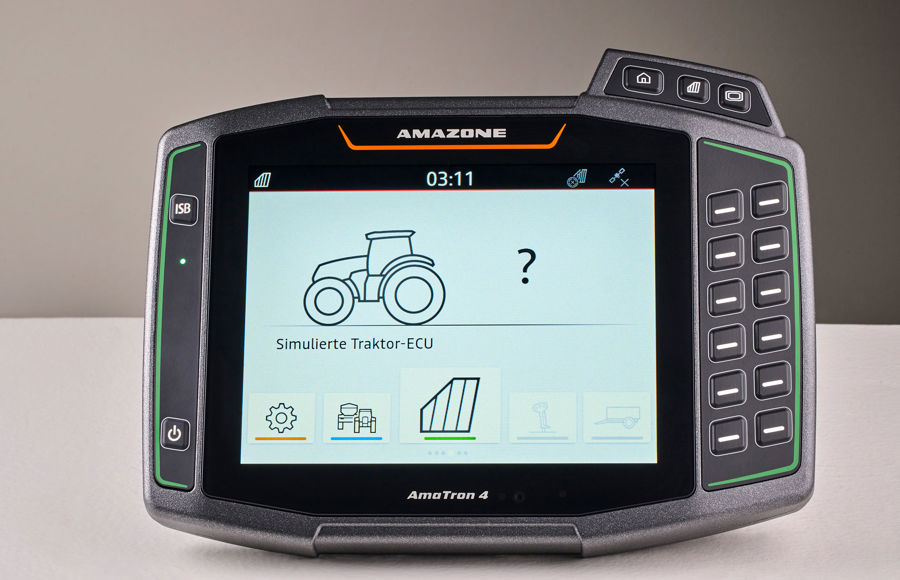
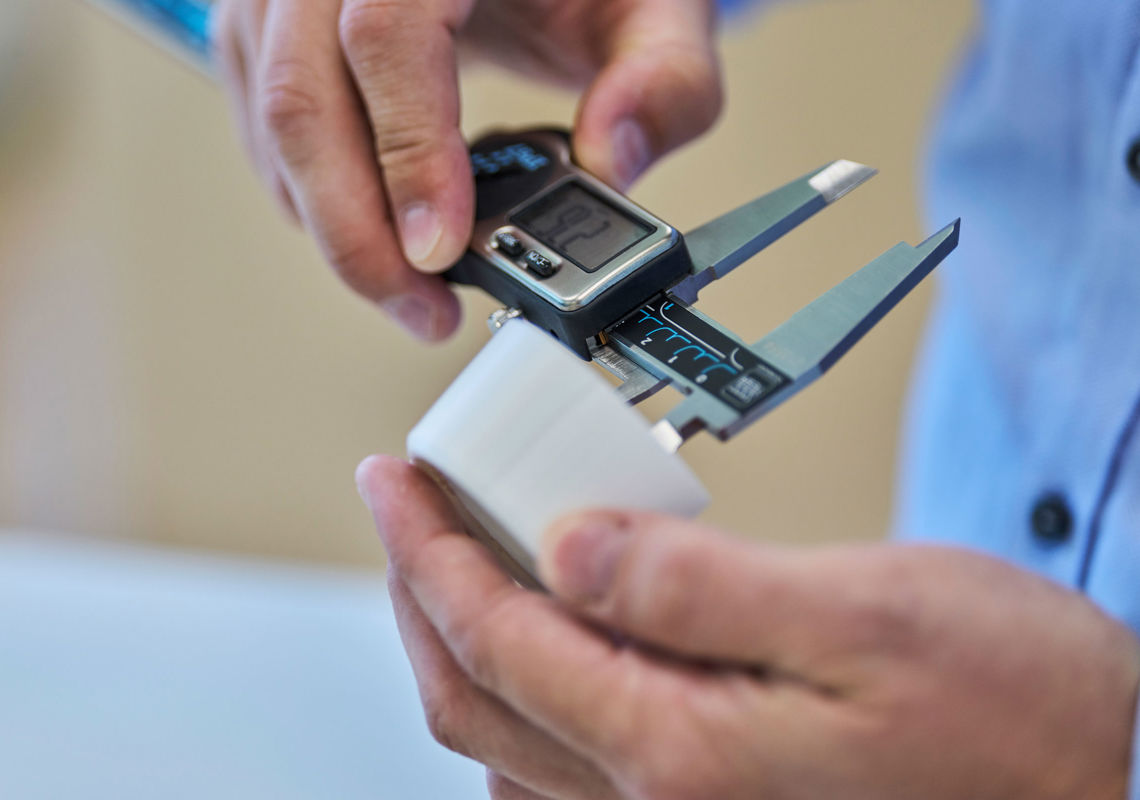
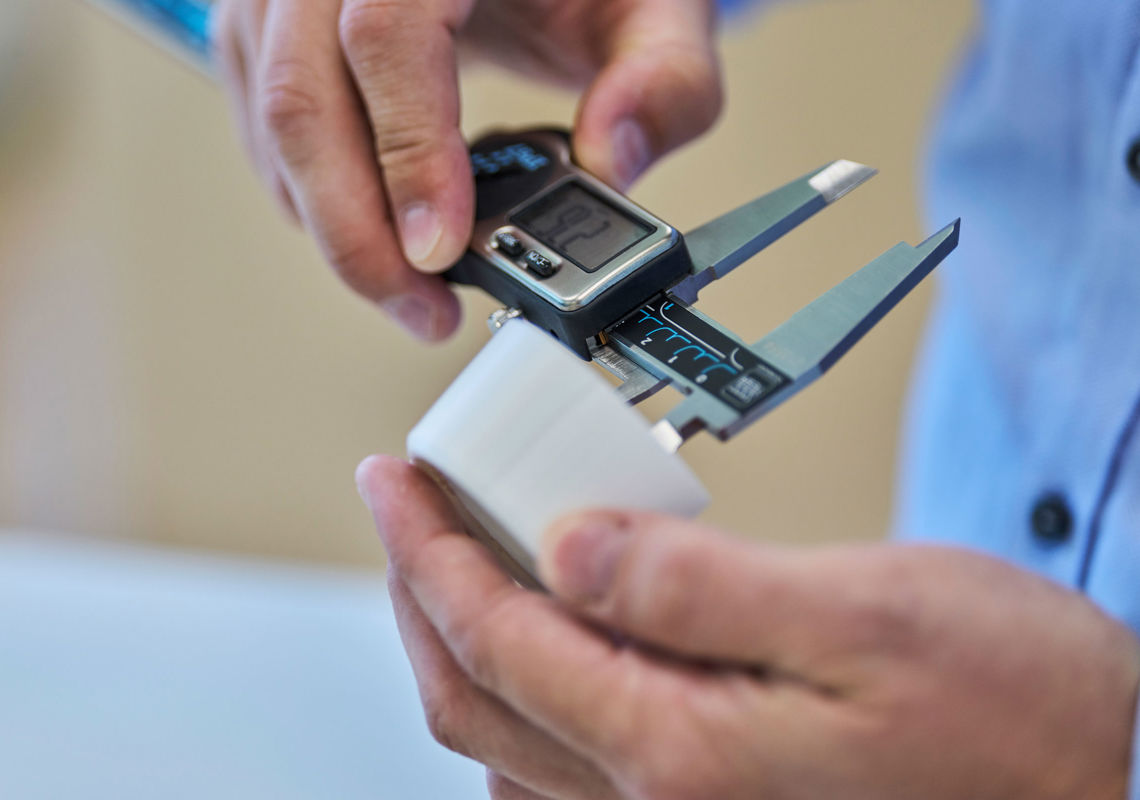
